Customized CNC Turning and Milling Parts Manufacturer from China
By:Admin
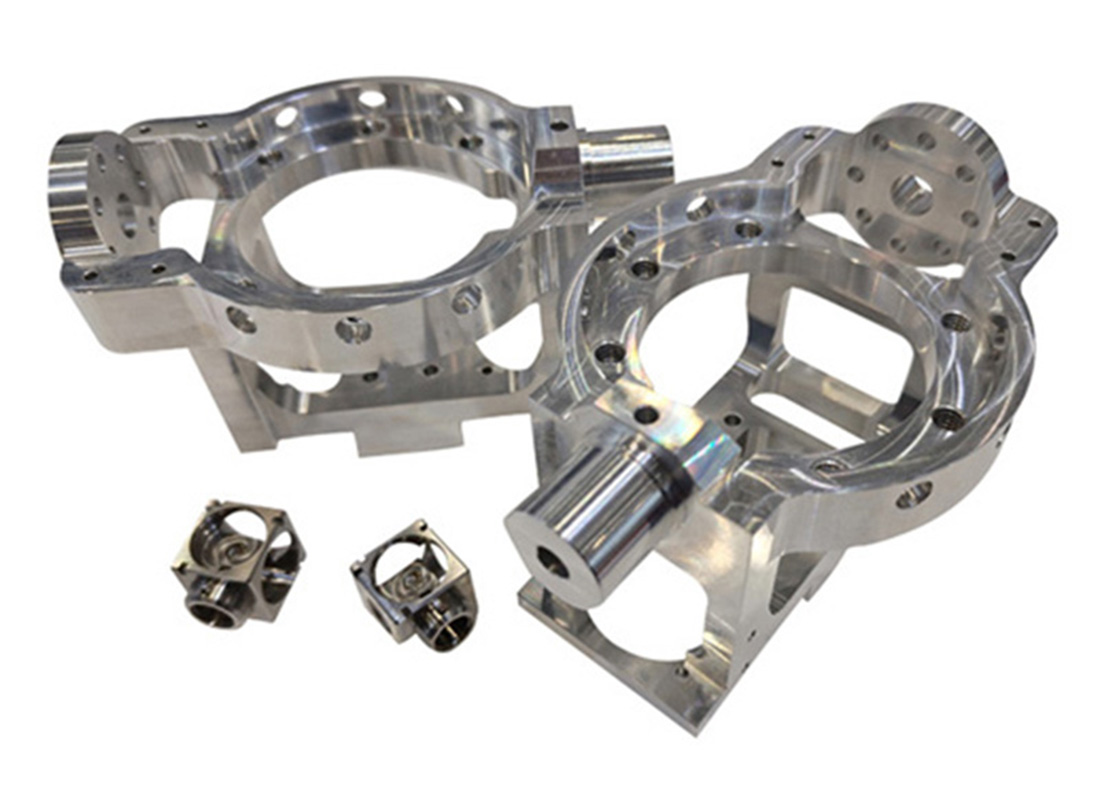
With a strong emphasis on quality, precision, and customer satisfaction, our company has established itself as a trusted provider of CNC turning and milling parts for a wide range of industries, including automotive, aerospace, medical, and electronics. Our state-of-the-art manufacturing facilities, advanced machinery, and skilled workforce enable us to produce a diverse range of high-precision components that meet the stringent requirements of our global clientele.
As a leading CNC turning parts manufacturer, we specialize in producing a wide variety of components, including shafts, bushings, connectors, and fasteners, among others. Our CNC turning process allows us to create complex geometries and achieve tight tolerances with ease, ensuring that our parts meet the exact specifications of our customers. Additionally, our CNC milling capabilities enable us to machine intricate shapes and contours, providing our clients with highly customized solutions for their specific applications.
At our CNC milling parts factory, we prioritize innovation and continuous improvement in our manufacturing processes. Our team of skilled engineers and technicians leverages the latest CAD/CAM software and advanced machining techniques to optimize production efficiency and ensure the highest level of accuracy and consistency in our parts. This commitment to excellence has earned us a reputation as a reliable and responsive partner for companies seeking precision-engineered components.
In addition to our technical expertise, our company is also dedicated to upholding the highest standards of quality and reliability. We adhere to strict quality control measures at every stage of the production process, from raw material inspection to final product testing. This rigorous approach enables us to deliver CNC turning and milling parts that consistently exceed industry standards and exceed customer expectations.
Furthermore, our company is committed to sustainability and environmental responsibility. We have implemented eco-friendly manufacturing practices and comply with all relevant regulations and standards to minimize our environmental impact. By prioritizing sustainability, we aim to contribute to a more environmentally conscious and sustainable future for the manufacturing industry.
With our unwavering dedication to quality, precision, and customer satisfaction, our company has established itself as a trusted CNC turning parts manufacturer and CNC milling parts factory in China. Whether it's a small prototype run or a large-scale production order, we have the capabilities and expertise to deliver high-quality CNC parts that meet the most demanding requirements of our clients.
As we look towards the future, we remain committed to pushing the boundaries of innovation and excellence in CNC machining. By continuously investing in advanced technology, expanding our capabilities, and nurturing our talented workforce, we are poised to remain at the forefront of the industry and continue to provide our customers with the highest quality CNC turning and milling parts.
Company News & Blog
High-quality Plastic Molding Services for Precision Parts
Precision Plastic Molding, a leading manufacturer of high-quality plastic components, announced today its plans to expand its production facilities in response to increasing demand for its products.The company, which specializes in precision injection molding, serves a wide range of industries including automotive, consumer electronics, medical devices, and packaging. With a focus on quality and precision, Precision Plastic Molding has become known for its ability to produce complex and intricate plastic components with tight tolerances.The expansion of its production facilities is part of the company's strategic growth plan to meet the growing demand for its products. The new facilities will enable Precision Plastic Molding to increase its production capacity and enhance its capabilities to serve its customers more effectively."We are excited to announce the expansion of our production facilities," said the CEO of Precision Plastic Molding. "This expansion is a testament to our commitment to providing the highest quality plastic components to our customers. By investing in new technologies and increasing our production capacity, we will be able to meet the growing demand for our products and better serve our customers."The new facilities will be equipped with state-of-the-art injection molding machines, robotics, and other advanced manufacturing technologies to ensure maximum efficiency and precision in the production process. In addition, the company plans to implement advanced quality control systems to maintain the highest standards of quality and consistency in its products."We are dedicated to continuous improvement and innovation in our manufacturing processes," said the CEO. "By investing in the latest technologies and equipment, we are confident that we will be able to maintain our competitive edge in the market and continue to provide our customers with the best plastic components available."The expansion of its production facilities is expected to create new job opportunities in the local community and contribute to the economic growth of the region. Precision Plastic Molding is committed to being a responsible corporate citizen and plans to work closely with local authorities and community organizations to ensure that the expansion project is completed in a sustainable and environmentally friendly manner.In addition to expanding its production facilities, Precision Plastic Molding is also investing in research and development to further enhance its product offerings and explore new opportunities in emerging markets. The company has a team of skilled engineers and designers who are dedicated to creating innovative solutions for its customers' most challenging applications."We are constantly striving to push the boundaries of what is possible with plastic injection molding," said the CEO. "Our investment in research and development will enable us to develop new products and solutions that will provide added value to our customers and help us to stay ahead of the competition."Precision Plastic Molding has built a strong reputation for delivering high-quality plastic components to its customers and is committed to maintaining its position as a leader in the industry. With the expansion of its production facilities and continued investment in innovation, the company is poised to meet the evolving needs of its customers and achieve sustainable growth in the years to come."We are confident that the expansion of our production facilities and our ongoing commitment to innovation will enable us to continue to exceed our customers' expectations and drive our company forward," said the CEO. "We are excited about the future and are looking forward to the opportunities that lie ahead."About Precision Plastic Molding - Precision Plastic Molding is a leading manufacturer of precision plastic components for a wide range of industries. With a focus on quality and precision, the company has built a strong reputation for delivering high-quality products to its customers. Precision Plastic Molding is committed to continuous improvement and innovation in its manufacturing processes, and is dedicated to providing the best plastic components available.
The Benefits of Rapid Injection Molding Prototyping
Rapid injection molding prototyping is a critical part of the product development process for many companies. It allows businesses to quickly and cost-effectively create prototypes of their products, enabling them to iterate and improve upon their designs before moving into full-scale production.One company that has been at the forefront of this technology is {}. Founded in 2005, {} has been providing rapid injection molding prototyping services to a wide range of industries, including automotive, aerospace, consumer electronics, and medical devices. With state-of-the-art facilities and a team of experienced engineers and technicians, {} has earned a reputation for delivering high-quality, precision prototypes in record time.One of the key benefits of rapid injection molding prototyping is speed. Traditional prototyping methods, such as CNC machining or 3D printing, can be time-consuming and costly. With rapid injection molding, companies can receive functional prototypes in a matter of days, allowing them to quickly test and validate their designs. This rapid turnaround time can be crucial in today's fast-paced business environment, where time-to-market is often a competitive advantage.Another advantage of rapid injection molding prototyping is its ability to produce high-quality, production-grade prototypes. By using the same materials and processes as full-scale production, companies can ensure that their prototypes accurately represent the final product. This level of fidelity is essential for testing the functionality, fit, and performance of a product, as well as for gathering valuable feedback from stakeholders and potential customers.In addition to speed and quality, rapid injection molding prototyping also offers cost savings. By eliminating the need for expensive tooling and long lead times, companies can significantly reduce the upfront investment required for prototype development. This allows businesses to explore multiple design iterations and make necessary adjustments without breaking the bank.{} has been a trusted partner for many companies looking to leverage the benefits of rapid injection molding prototyping. The company's team of experts works closely with clients to understand their specific needs and requirements, providing valuable guidance and support throughout the prototyping process. Whether it's a complex automotive part or a delicate medical device, {} has the knowledge and capabilities to deliver reliable, high-precision prototypes.To further enhance its prototyping services, {} has continued to invest in advanced technologies and processes. The company regularly updates its equipment and software to ensure that it remains at the forefront of the industry. By staying abreast of the latest developments in rapid injection molding, {} is able to offer its clients the most innovative and effective prototyping solutions available.With a strong track record of delivering exceptional results, {} has become a go-to partner for companies seeking rapid injection molding prototyping services. Its commitment to quality, speed, and cost-effectiveness has earned {} a loyal customer base and a reputation as a leader in the prototyping industry.As the demand for rapid injection molding prototyping continues to grow, {} is well-positioned to meet the needs of businesses across a wide range of industries. With its unwavering dedication to customer satisfaction and its relentless pursuit of excellence, {} is poised to remain a top choice for companies seeking high-quality, reliable prototyping services.
Ultimate Guide to Laser Cutting Polyethylene Foam: Everything You Need to Know
Laser Cutting Polyethylene Foam Revolutionizes Packaging IndustryIn today's fast-paced world, businesses are constantly seeking innovative solutions to improve their products and services. One company at the forefront of this innovation is {Company name}, a leading provider of advanced packaging solutions. Recently, {Company name} has introduced a groundbreaking method for cutting polyethylene foam with laser technology, a game-changing development that is set to revolutionize the packaging industry.Polyethylene foam is widely used in packaging due to its lightweight, durable, and versatile nature. It is commonly utilized for cushioning and protecting a wide range of products during transit and storage. However, traditional methods of cutting and shaping polyethylene foam often involve time-consuming processes that are not always precise or cost-effective.{Company name} saw an opportunity to enhance the efficiency and quality of polyethylene foam cutting by leveraging state-of-the-art laser technology. By integrating laser cutting systems into their production process, they have achieved unparalleled precision, speed, and flexibility in shaping polyethylene foam, setting a new standard for the industry.The advanced laser cutting technology utilized by {Company name} allows for intricate designs and complex patterns to be effortlessly and accurately cut into polyethylene foam, providing a level of customization and detail that was previously unattainable. This capability opens up a world of possibilities for packaging designers and manufacturers, enabling them to create unique and tailored solutions to meet the specific needs of their products and customers.In addition to its precision and flexibility, laser cutting polyethylene foam offers environmental benefits as well. The process produces minimal waste and emissions, contributing to a more sustainable and eco-friendly approach to packaging production. As sustainability continues to be a key focus for businesses across the globe, this innovation aligns with the growing demand for environmentally responsible solutions.{Company name}'s investment in laser cutting technology for polyethylene foam underscores its commitment to providing cutting-edge packaging solutions to its clients. With a strong emphasis on innovation and continuous improvement, the company is dedicated to staying ahead of the curve and meeting the evolving needs of the packaging industry.This latest development further solidifies {Company name} as a leader in the packaging sector, building on its track record of delivering high-quality products and exceptional customer service. With a focus on collaboration and partnership, {Company name} works closely with its clients to understand their unique challenges and requirements, offering innovative solutions that add value and drive success.Furthermore, by incorporating laser cutting technology, {Company name} is not only enhancing the capabilities of its own manufacturing processes but also providing its clients with a competitive advantage in the market. The ability to create distinct and tailored packaging solutions through laser-cut polyethylene foam sets them apart from the competition, enabling them to stand out and make a lasting impression on their customers.Moving forward, {Company name} envisions continued advancements in laser cutting technology for polyethylene foam, ushering in a new era of possibilities for the packaging industry. With a focus on research and development, the company aims to push the boundaries of what is achievable, seeking to innovate and refine its processes to better serve its clientele.In conclusion, {Company name}'s introduction of laser cutting polyethylene foam represents a significant milestone for the packaging industry. With its unrivaled precision, flexibility, and environmental benefits, this advancement is poised to reshape the way packaging is designed and manufactured. As businesses strive to differentiate themselves in the market, the ability to leverage laser-cut polyethylene foam for customized and sustainable packaging solutions will undoubtedly be a game-changer. As {Company name} continues to lead the way in innovation, the future of packaging looks brighter than ever.
Understanding the Process of Short Run Injection Molding
Short Run Injection Molding: A Game-Changer in ManufacturingIn the world of manufacturing, efficiency and speed are key. Companies are constantly seeking new ways to streamline their production processes and bring products to market faster. One technology that has emerged as a game-changer in manufacturing is short run injection molding.Fast. Reliable. Cost-effective. These are just a few of the words to describe short run injection molding. It is a manufacturing process that allows for the production of small to medium-sized batches of parts and products with a fast turnaround time.One company that has been at the forefront of short run injection molding is {}. They have been providing innovative solutions for manufacturers across various industries, from automotive to consumer goods, and have become a trusted partner for companies looking to accelerate their production timelines.{} has built a reputation for excellence in the world of injection molding. Their state-of-the-art facilities and expert team of engineers and technicians have enabled them to produce high-quality parts and products quickly and efficiently. They have invested heavily in cutting-edge machinery and technology, allowing them to offer a wide range of services, including rapid prototyping, tooling, and production.One of the key advantages of short run injection molding is its ability to reduce time-to-market for new products. With traditional manufacturing processes, companies often face long lead times and high setup costs, making it difficult to iterate and improve on designs quickly. Short run injection molding solves this problem by allowing for the rapid production of prototypes and small batches of products, enabling companies to test and refine their designs before scaling up for mass production.Another advantage of short run injection molding is its cost-effectiveness. By only producing the necessary quantities of parts and products, companies can avoid the high tooling costs associated with traditional manufacturing processes. This is particularly beneficial for small and medium-sized businesses that may not have the resources to invest in large production runs.In addition, short run injection molding offers flexibility and scalability. Companies can easily adjust their production volumes based on market demand, without having to commit to large production runs. This agility allows for faster response times to market trends and customer needs, giving companies a competitive edge in today's fast-paced business environment.The applications for short run injection molding are vast and diverse. From medical devices to consumer electronics, automotive components to industrial machinery, the technology is being used across a wide range of industries. Whether it's for producing prototypes, low-volume production runs, or on-demand manufacturing, short run injection molding has proven to be a versatile and invaluable tool for companies looking to stay ahead of the curve.As the demand for short run injection molding continues to grow, companies like {} are poised to play a crucial role in shaping the future of manufacturing. With their commitment to innovation, quality, and customer satisfaction, they are well-positioned to meet the evolving needs of the market and drive new advancements in the industry.In conclusion, short run injection molding has revolutionized the way companies approach manufacturing. By offering speed, reliability, and cost-effectiveness, it has become an essential tool for bringing products to market faster and more efficiently. As the technology continues to evolve, companies like {} will continue to lead the way in delivering innovative solutions that help businesses thrive in today's competitive landscape.
Rapid Prototyping Innovations in Mechanical Engineering
Rapid prototyping is revolutionizing the field of mechanical engineering, allowing companies to quickly and cost-effectively develop and test new products. With the help of cutting-edge technologies and innovative approaches, mechanical engineers are now able to produce functional prototypes in a fraction of the time it used to take, ultimately speeding up the overall design process.One company that has been at the forefront of this revolution is {}. With a passion for pushing the boundaries of what's possible in mechanical engineering, they have been using rapid prototyping to bring their ideas to life in record time. By leveraging advanced 3D printing and additive manufacturing techniques, they have been able to create complex and intricate prototypes with ease, helping them stay ahead of the competition.With rapid prototyping, mechanical engineers are able to produce physical prototypes of their designs within hours or days, rather than weeks or months. This acceleration in the design process allows them to iterate and refine their concepts much more quickly, ultimately leading to better end products. By being able to physically hold and test their prototypes early in the design process, engineers can catch potential flaws and make improvements before going into full production, saving time and resources in the long run.In addition to speeding up the design and testing phase, rapid prototyping also allows for a more flexible and iterative approach to product development. Engineers can easily make adjustments to their designs and produce updated prototypes on the fly, without having to invest in expensive tooling or manufacturing processes. This agility is especially valuable in today's fast-paced business world, where companies need to adapt quickly to changing market demands and technological advancements.The use of rapid prototyping in mechanical engineering has also opened up new possibilities for innovation and creativity. With the ability to create prototypes with intricate geometries and complex internal structures, engineers are now able to explore designs that were previously impossible to manufacture using traditional methods. This has led to the development of new kinds of products that are more efficient, functional, and aesthetically pleasing than ever before.While rapid prototyping has already had a profound impact on mechanical engineering, the technology is still evolving. Cutting-edge companies like {} are constantly pushing the boundaries of what's possible, developing new materials and processes that further enhance the capabilities of rapid prototyping. As these advancements continue to emerge, the potential for innovation in mechanical engineering will only continue to grow.In conclusion, rapid prototyping has become an essential tool for mechanical engineers, allowing them to iterate, innovate, and ultimately bring better products to market in less time. With the help of companies like {}, the field of mechanical engineering is poised for even more exciting advancements in the years to come. As the technology continues to evolve, we can expect to see even more groundbreaking innovations that will shape the future of product design and manufacturing.
Top Tips for Successful Injection Molding
Injection molding is a highly versatile method used in the manufacturing industry to produce a wide range of products and components. This process involves melting a thermoplastic material and injecting it into a mold cavity, where it is then cooled and solidified to form the desired shape. One company at the forefront of injection molding technology is {}. With their state-of-the-art facilities and advanced machinery, they have been able to offer innovative solutions to their clients across various industries. {} has built a strong reputation for delivering high-quality products and components using injection molding. They have a team of experienced engineers and technicians who work closely with clients to understand their specific requirements and provide customized solutions. From design and prototyping to production and assembly, {} offers a comprehensive range of services to meet the needs of their clients. The company is committed to staying ahead of the curve when it comes to injection molding technology. They continuously invest in the latest machinery and equipment to ensure that they are able to deliver precise and efficient manufacturing solutions. This commitment to innovation has enabled {} to stay competitive in the market and maintain their position as a leading provider of injection molded products.In addition to their technical capabilities, {} also places a strong emphasis on quality control and process optimization. They have implemented strict quality management systems to ensure that each product that comes out of their facility meets the highest standards. This dedication to quality has earned them the trust and confidence of their clients, who rely on {} to deliver reliable and durable products.{} serves a diverse range of industries, including automotive, consumer electronics, medical, and more. Their ability to cater to the unique needs of each industry and provide tailored solutions sets them apart from their competitors. Whether it's manufacturing precision components for the automotive sector or producing medical devices with strict regulatory requirements, {} has the expertise and resources to deliver on their clients' expectations.As a responsible corporate citizen, {} is also committed to sustainability and environmental responsibility. They have implemented eco-friendly practices in their manufacturing processes and strive to minimize their environmental footprint. By using recyclable materials and optimizing their energy consumption, {} is dedicated to reducing their impact on the environment while still delivering exceptional products.Looking towards the future, {} is poised to continue leading the way in injection molding technology. They are continuously exploring new materials, processes, and techniques to improve their capabilities and expand their offerings. By staying at the forefront of technological advancements, {} is well-positioned to meet the evolving needs of their clients and remain a trusted partner in the manufacturing industry.In conclusion, injection molding is a crucial process in the manufacturing industry, and {} has established itself as a key player in this field. With their commitment to innovation, quality, and sustainability, they have earned a strong reputation and a loyal client base. As they continue to invest in their capabilities and adapt to the changing industry landscape, {} is well-prepared to maintain their leadership position and drive the future of injection molding technology.
Diverse Metal Fabrication: A Comprehensive Guide to Superior Metalwork
The art of metal fabrication has been revolutionized in recent years thanks to the innovative techniques developed by (company name). By using state-of-the-art technology and a highly skilled workforce, the company has become a leader in the complex metal fabrication industry.Founded in (year), (company name) has quickly gained a reputation for its precision and attention to detail in every project. Their facility, located in (location), is equipped with the latest machinery and tools, allowing them to take on a wide range of complex metal fabrication projects.One of the key features of (company name) is its ability to work with a variety of metals, including stainless steel, aluminum, and titanium. This versatility has allowed them to cater to a diverse clientele, ranging from the aerospace industry to the automotive sector.One of the most notable aspects of (company name) is its commitment to quality control. Every step of the fabrication process is carefully monitored to ensure that the final product meets the highest standards. This dedication to excellence has earned them the trust of their clients, who rely on them to deliver top-notch products every time.In addition to their technical prowess, (company name) also prides itself on its ability to provide customized solutions for its clients. Whether it's a one-of-a-kind prototype or a large-scale production run, the team at (company name) is dedicated to fulfilling the unique needs of each customer.Furthermore, their team of experienced engineers and designers work closely with clients from the initial concept to the final product, ensuring that every detail is precisely executed. This collaborative approach has resulted in many successful projects and lasting partnerships with numerous clients.One of the most recent projects undertaken by (company name) was the fabrication of a complex metal component for a leading aerospace company. The client required a high-strength, lightweight component for their new aircraft, and (company name) was able to deliver a flawless solution that exceeded their expectations.The success of this project has further solidified (company name)'s reputation as a premier provider of complex metal fabrication services. With each successful project, they continue to raise the bar for the industry and set new standards for excellence.Looking ahead, (company name) is committed to further expanding its capabilities and enhancing its technological infrastructure. They are constantly investing in the latest equipment and training their workforce to stay ahead of the curve in an ever-evolving industry.In conclusion, (company name) has established itself as a leading force in the complex metal fabrication industry, thanks to its unwavering commitment to quality, precision, and innovation. With a track record of successful projects and a strong focus on customer satisfaction, the company is poised to continue its upward trajectory and remain at the forefront of the industry for years to come.
The Ultimate Guide to Laser-Cut Foam Board: Tips, Techniques, and Benefits
Laser Cut Foam Board: Revolutionizing the IndustryIn the ever-evolving world of design and manufacturing, staying ahead of the curve is essential for companies seeking to remain competitive. This is especially true for the [Company Name], a leading provider of high-quality foam board solutions. The company has recently announced the launch of a new product that is set to revolutionize the industry – Laser Cut Foam Board.Laser Cut Foam Board is a cutting-edge material that combines the versatility of foam board with the precision of laser cutting technology. This innovative product offers a wide range of benefits, making it ideal for a variety of applications in industries such as packaging, signage, and model making.One of the key advantages of Laser Cut Foam Board is its high level of precision. The use of laser cutting technology ensures that each piece is cut to exact specifications, resulting in a perfect fit every time. This level of precision is especially important in industries where accuracy is paramount, such as in the creation of intricate packaging designs or detailed signage.Another benefit of Laser Cut Foam Board is its versatility. The material is available in a variety of thicknesses and colors, making it suitable for a wide range of applications. Whether it's creating eye-catching displays or building detailed architectural models, Laser Cut Foam Board offers the flexibility needed to bring any design to life.In addition to its precision and versatility, Laser Cut Foam Board also offers superior durability. The material is resistant to moisture, chemicals, and aging, ensuring that it can withstand the rigors of daily use without deteriorating. This durability makes it an ideal choice for long-lasting applications, such as outdoor signage or protective packaging.The introduction of Laser Cut Foam Board reflects [Company Name]'s commitment to innovation and meeting the changing needs of its customers. The company has a long history of providing high-quality foam board solutions, and the launch of this new product further solidifies its position as a leader in the industry.With a state-of-the-art manufacturing facility and a team of skilled professionals, [Company Name] is well-equipped to produce Laser Cut Foam Board to the highest standards. The company's dedication to quality and customer satisfaction ensures that each piece of Laser Cut Foam Board meets the strictest industry standards, providing customers with confidence in the reliability and performance of the product.In addition to its commitment to quality, [Company Name] is also dedicated to environmental sustainability. Laser Cut Foam Board is a recyclable material, underscoring the company's commitment to reducing its impact on the environment. By offering a product that is both high-performing and environmentally friendly, [Company Name] is taking a proactive approach to corporate responsibility.As [Company Name] continues to drive innovation in the foam board industry, the launch of Laser Cut Foam Board represents a significant milestone in the company's history. With its unparalleled precision, versatility, and durability, this new product is poised to revolutionize the way designers and manufacturers approach their projects. The introduction of Laser Cut Foam Board underscores [Company Name]'s position as a leader in the industry and sets a new standard for foam board solutions.With its cutting-edge technology and unwavering commitment to quality, [Company Name] is paving the way for a new era of design and manufacturing. As the company continues to push the boundaries of what is possible, one thing is certain – the future is bright for both [Company Name] and the industries it serves.
Benefits of Small Run Injection Molding for Manufacturing
Small Run Injection Molding (SRI) is a leading manufacturing company specialized in providing high-quality plastic injection molding solutions for small to medium-sized production runs. With a strong focus on quality, precision, and customer satisfaction, SRI has established a solid reputation in the industry for delivering exceptional products to various clients across different sectors.Established over a decade ago, SRI has continuously evolved and expanded its capabilities to meet the ever-growing demands of the market. The company’s state-of-the-art manufacturing facility is equipped with advanced injection molding machines, cutting-edge technologies, and a team of highly skilled professionals who are dedicated to delivering outstanding results. As a full-service provider, SRI offers a comprehensive range of services including product design, tooling, prototyping, and production.SRI takes pride in its ability to cater to the unique needs of its clients, offering flexible solutions that are tailored to their specific requirements. Whether it’s a small batch of custom-designed parts or a medium-sized production run, the company is committed to delivering superior quality products with a quick turnaround time. SRI's expertise in small run injection molding allows businesses to bring their concepts to life and get their products to market in a cost-effective and efficient manner.One of the key differentiators for SRI is its dedication to maintaining the highest standards of quality throughout the production process. The company follows strict quality control protocols to ensure that every product that comes out of its facility meets the exacting specifications of its clients. This commitment to quality has earned SRI the trust and loyalty of its customers, who rely on the company for consistent, reliable, and top-notch results.Additionally, SRI places a strong emphasis on innovation and continuous improvement. The company stays abreast of the latest advancements in injection molding technology and regularly invests in upgrading its infrastructure to stay ahead of the curve. This proactive approach enables SRI to take on challenging projects, push the boundaries of what is possible in injection molding, and deliver innovative solutions to its clients.In line with its commitment to sustainability, SRI also places a high priority on environmental responsibility. The company utilizes eco-friendly materials and processes wherever possible, minimizing its ecological footprint while still delivering high-quality products. By adopting sustainable practices, SRI is contributing to a more environmentally conscious approach to manufacturing.SRI has earned recognition for its excellence in manufacturing and has received accolades for its exceptional performance, reliability, and customer satisfaction. The company's dedication to its craft and its unwavering commitment to exceeding customer expectations have positioned it as a trusted partner for businesses seeking top-tier injection molding solutions.Overall, Small Run Injection Molding (SRI) stands out as a prime example of a manufacturing company that excels in delivering high-quality, precision-engineered products for small to medium-sized production runs. With its focus on innovation, quality, and customer satisfaction, SRI continues to solidify its position as a leader in the injection molding industry, setting new benchmarks for excellence and reliability. Whether it's a custom project or a standard production run, SRI is the go-to choice for businesses looking for exceptional injection molding solutions.
High Precision CNC Mill for Superior Machining
High Precision CNC Mill Revolutionizes Manufacturing IndustryWith the continuous advancement in technology, the manufacturing industry is witnessing a significant transformation. The introduction of high precision CNC mills has taken manufacturing to a new level, enabling companies to produce complex and intricate components with unparalleled precision and accuracy. One such company at the forefront of this technological revolution is {}, a leading manufacturer of advanced CNC machines. With a strong focus on innovation and quality, the company has been driving the industry forward with its cutting-edge technology and state-of-the-art solutions.The high precision CNC mill developed by {} has set a new benchmark in the industry, offering unmatched levels of precision and efficiency. This advanced machine is equipped with the latest control systems and cutting-edge software, allowing for seamless integration of complex designs and precise machining operations. The result is a finished product that meets the highest standards of quality and accuracy.One of the key features of the high precision CNC mill is its ability to produce components with tight tolerances and intricate geometries. This has opened up new possibilities for companies across a wide range of industries, including aerospace, automotive, medical, and electronics. The ability to produce complex parts with high precision has enabled manufacturers to push the boundaries of what is possible, leading to innovation and advancements in various sectors.In addition to its precision capabilities, the CNC mill also offers high levels of productivity and efficiency. The advanced automation features and powerful cutting tools allow for rapid production of components, reducing lead times and increasing overall throughput. This has led to significant improvements in manufacturing processes, resulting in higher productivity and cost savings for companies utilizing this technology.Another important aspect of the high precision CNC mill is its versatility. It is capable of machining a wide range of materials, including metals, plastics, and composites, making it suitable for a variety of applications. This flexibility has made the CNC mill a valuable asset for companies looking to expand their capabilities and take on a diverse range of projects.Furthermore, the CNC mill has been designed with user-friendly interfaces and intuitive controls, making it easy for operators to set up, program, and monitor machining operations. This has reduced the learning curve for operators, allowing them to quickly adapt to the new technology and maximize its potential.Moreover, the high precision CNC mill is equipped with advanced safety features to ensure a secure working environment for operators. With built-in sensors and safety protocols, the machine is able to detect and respond to potential hazards, minimizing the risk of accidents and injuries in the workplace.{} has also been proactive in providing comprehensive training and support for its customers, ensuring that they have the knowledge and resources to fully utilize the capabilities of the high precision CNC mill. This commitment to customer satisfaction has helped the company build a strong reputation in the industry, with a track record of delivering reliable and high-performance machines.Overall, the introduction of high precision CNC mills has been a game-changer for the manufacturing industry, offering a level of precision, efficiency, and versatility that was previously unattainable. As technology continues to evolve, the potential for further advancements in CNC machining is limitless, and companies like {} are leading the way in shaping the future of manufacturing.