Rapid Prototyping Mold: A Guide to Fast Mold Creation for Manufacturing
By:Admin
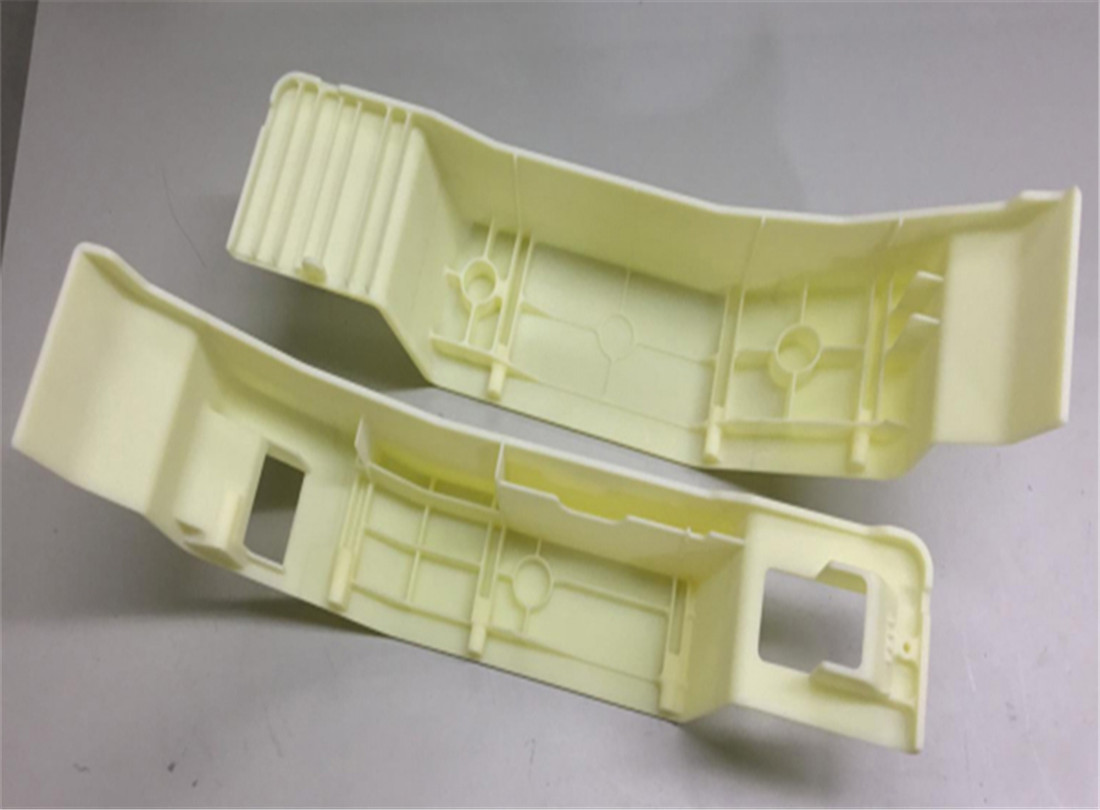
In today's fast-paced and competitive manufacturing industry, the ability to quickly and efficiently produce high-quality molds is essential. This is where rapid prototyping molds come into play, revolutionizing the way products are designed and manufactured. With their speed, precision, and cost-effectiveness, rapid prototyping molds are changing the game for businesses across various sectors.
One company at the forefront of this game-changing technology is [Company Name]. With over [number of years] of experience in the manufacturing industry, [Company Name] has established itself as a leading provider of rapid prototyping molds, catering to the needs of businesses looking to streamline their production processes and bring innovative products to market faster than ever before.
Rapid prototyping molds, also known as 3D printing molds, are created using advanced additive manufacturing techniques. This allows for the rapid production of custom molds with intricate designs and complex geometries that traditional manufacturing methods struggle to achieve. The result is a significant reduction in lead times and costs, as well as the ability to iterate and refine designs more quickly and with greater accuracy.
[Company Name] has invested heavily in state-of-the-art 3D printing technology, enabling them to offer their clients a wide range of rapid prototyping mold solutions. From small-scale molds for plastic injection molding to larger molds for metal casting, [Company Name] can meet the diverse needs of businesses operating in various industries, such as automotive, aerospace, consumer goods, and more.
One of the key advantages of rapid prototyping molds is their ability to accelerate the product development cycle. By quickly producing molds for prototype parts, businesses can test and validate their designs much earlier in the process, leading to faster iterations and ultimately, a shorter time to market. This is particularly beneficial for companies looking to stay ahead of the competition and capitalize on emerging opportunities in their respective markets.
Furthermore, rapid prototyping molds offer unparalleled design freedom. Unlike traditional molds that are limited by manufacturing constraints, 3D printing molds allow for highly complex and intricate designs to be realized with ease. This opens up new possibilities for product innovation and customization, giving businesses the flexibility to create unique and highly functional products that stand out in the marketplace.
In addition to their speed and flexibility, rapid prototyping molds also offer cost advantages. With traditional mold-making methods, the cost of creating custom molds can be prohibitively high, especially for small production runs. Rapid prototyping molds, on the other hand, significantly reduce the upfront costs associated with mold production, making it more accessible for businesses of all sizes to bring their ideas to life.
The benefits of rapid prototyping molds are clear, and businesses that embrace this technology are poised to gain a competitive edge in the market. By partnering with a trusted and experienced provider like [Company Name], businesses can harness the power of rapid prototyping molds to accelerate their product development, reduce costs, and ultimately, drive innovation in their respective industries.
Looking ahead, the potential for rapid prototyping molds to transform the manufacturing landscape is immense. As the technology continues to evolve and improve, businesses will have even greater opportunities to push the boundaries of what's possible in product design and production. With [Company Name] leading the way in this exciting field, the future of manufacturing looks brighter than ever.
Company News & Blog
Custom CNC Milled Radiator Enclosure: The Latest Innovation in Thermal Management Technology
CNC Milled Radiator Enclosure: A Game Changer in Metal Manufacturing[Company Name], a leading manufacturer of precision metal components, has recently introduced a groundbreaking product in the field of metal manufacturing - the CNC milled radiator enclosure. This innovative product is set to revolutionize the way metal components are produced and is already generating a significant buzz in the industry.The CNC milled radiator enclosure is a result of years of research and development by the dedicated team at [Company Name]. It is designed to provide outstanding performance and durability, making it the ideal choice for a wide range of applications in the automotive, aerospace, and manufacturing industries. The radiator enclosure is produced using state-of-the-art CNC milling machines, ensuring a level of precision and accuracy that is unmatched by traditional manufacturing methods.One of the key features of the CNC milled radiator enclosure is its exceptional heat dissipation capabilities. The unique design of the enclosure allows for efficient cooling of the radiator, ensuring optimal performance and longevity. This is especially important in industries where high temperatures and thermal management are critical factors.In addition to its superior performance, the CNC milled radiator enclosure also offers significant cost savings compared to alternative manufacturing methods. By utilizing advanced CNC milling techniques, [Company Name] is able to produce the enclosure with minimal material waste and reduced production time. This means that customers can benefit from a high-quality, precision-engineered product at a competitive price point.Furthermore, the CNC milled radiator enclosure is manufactured using high-grade materials that are known for their strength and resilience. This ensures that the enclosure can withstand the rigors of demanding industrial applications, making it a reliable and long-lasting solution for our customers.The introduction of the CNC milled radiator enclosure further solidifies [Company Name]’s reputation as an industry leader in metal manufacturing. With a commitment to continuous innovation and excellence, the company has established itself as a trusted partner for businesses seeking top-quality metal components.Customers can also take advantage of [Company Name]’s in-house engineering and design services to customize the CNC milled radiator enclosure to meet their specific requirements. The company’s team of experienced engineers can work closely with customers to develop tailored solutions that address their unique challenges and deliver exceptional results.As a testament to its commitment to quality and customer satisfaction, [Company Name] adheres to strict quality control measures throughout the production process. This ensures that every CNC milled radiator enclosure that leaves the facility meets the highest standards of excellence.In conclusion, the introduction of the CNC milled radiator enclosure by [Company Name] is a significant milestone in the field of metal manufacturing. With its cutting-edge design, exceptional performance, and cost-effective production, this innovative product is set to redefine the industry standards for precision metal components. With a focus on excellence and customer-centric innovation, [Company Name] continues to lead the way in delivering superior solutions for businesses across a wide range of industries.
Leading Manufacturer of Silicon Parts: Advantages and Applications
Silicone Parts Manufacturer Leads the Industry with Innovative Technology and Quality ProductsAs the demand for silicone parts continues to rise in various industries, one company has been at the forefront of innovation and quality manufacturing. With a commitment to excellence and a focus on customer satisfaction, [Silicone Parts Manufacturer] has established itself as a leader in the industry.Based in [Location], [Silicone Parts Manufacturer] has been serving customers around the world for over [number] years. The company specializes in the design and production of high-quality silicone parts for a wide range of applications, including automotive, medical, aerospace, and consumer electronics.One of the key factors that sets [Silicone Parts Manufacturer] apart from its competitors is its dedication to innovation. The company invests heavily in research and development to stay ahead of the curve and to continually improve its products and processes. This commitment to innovation has led to the development of several groundbreaking technologies and manufacturing techniques that have revolutionized the industry.In addition to its innovative approach, [Silicone Parts Manufacturer] also prioritizes quality in every aspect of its operations. The company uses only the highest-grade materials and state-of-the-art equipment to ensure that its products meet the highest standards of excellence. From design and prototyping to production and inspection, every step of the manufacturing process is meticulously monitored to guarantee the utmost quality.Furthermore, [Silicone Parts Manufacturer] holds several certifications and accreditations, demonstrating its dedication to maintaining the highest levels of quality and safety. The company is ISO [Number] and [Other Certification] certified, which reflects its adherence to stringent quality management systems and industry best practices.One of the company's most notable achievements is its development of a proprietary silicone molding process, which allows for the production of complex and intricate parts with unparalleled precision and detail. This innovative technology has enabled [Silicone Parts Manufacturer] to offer customized solutions to meet the unique needs of its customers, setting it apart as a trusted partner for companies across diverse industries.In addition to its commitment to innovation and quality, [Silicone Parts Manufacturer] also places a strong emphasis on customer satisfaction. The company works closely with its clients to understand their specific requirements and to provide tailored solutions that meet and exceed their expectations. With a dedicated team of skilled professionals, [Silicone Parts Manufacturer] is able to offer comprehensive support and guidance throughout the entire product development and manufacturing process.As a result of its relentless pursuit of excellence, [Silicone Parts Manufacturer] has earned a reputation as a trusted and reliable partner in the industry. The company has established long-term relationships with many industry-leading companies, who rely on its expertise and capabilities to deliver superior silicone parts that are critical to their products and operations.Looking to the future, [Silicone Parts Manufacturer] remains committed to pushing the boundaries of innovation and quality in the silicone parts industry. The company continues to invest in research and development, with a focus on developing new technologies and materials that will further enhance its product offerings and manufacturing capabilities. Additionally, [Silicone Parts Manufacturer] is exploring opportunities to expand its presence in emerging markets and to further strengthen its position as a global leader in the industry.For companies seeking a trusted partner for high-quality silicone parts, [Silicone Parts Manufacturer] stands out as a proven industry leader that is dedicated to delivering excellence in every aspect of its operations. With its innovative technologies, uncompromising commitment to quality, and customer-centric approach, [Silicone Parts Manufacturer] is poised to continue setting the standard for excellence in the industry for years to come.
High-Quality Aluminum Die Casting Services for Various Industries
Aluminum Die Casting: A Game-Changer in the Manufacturing IndustryIn today's highly competitive manufacturing industry, companies are constantly seeking ways to improve efficiency, reduce costs, and enhance the overall quality of their products. One of the key technologies that has been making a significant impact in this regard is aluminum die casting. Featured as an integral part of the company’s manufacturing process, aluminum die casting has revolutionized the way products are made. With its ability to produce complex and intricately shaped parts with high precision, aluminum die casting has become the go-to method for many industries, including automotive, aerospace, and electronics.At the forefront of this industry-leading technology is {Company Name}, a renowned company with a sterling reputation for excellence in the field of aluminum die casting. With state-of-the-art facilities and a team of highly skilled professionals, {Company Name} has been leading the way in delivering high-quality aluminum die casting solutions to its clients.Aluminum die casting is a process that involves injecting molten aluminum into a steel mold, known as a die, at high pressures. This results in the production of parts that are extremely durable, with excellent mechanical properties and low porosity. The versatility of this process allows for the production of a wide range of complex shapes and sizes, making it an ideal choice for a variety of applications.One of the key advantages of aluminum die casting is its cost-effectiveness. The high-speed production capabilities and the ability to produce net-shaped parts with minimal secondary operations make it a highly efficient manufacturing process. This, in turn, leads to significant cost savings for companies, ultimately translating to a competitive edge in the market.Furthermore, the lightweight nature of aluminum makes it an ideal material for applications in industries such as automotive and aerospace, where weight reduction is a critical factor. Aluminum die cast parts offer high strength-to-weight ratios, making them an excellent choice for demanding applications that require both strength and durability.{Company Name} has been at the forefront of innovation in aluminum die casting, constantly pushing the boundaries of what is possible in terms of part complexity, precision, and quality. Their extensive experience in the industry, combined with their commitment to continuous improvement, has enabled them to consistently deliver exceptional results to their clients.The company's dedication to quality is reflected in their stringent quality control measures and adherence to industry standards. By utilizing advanced simulation and testing techniques, {Company Name} ensures that each part produced through aluminum die casting meets the highest standards of quality and performance.In addition to aluminum die casting, {Company Name} also offers a range of value-added services, including machining, finishing, and assembly. This comprehensive approach allows them to provide end-to-end solutions to their clients, further cementing their position as a trusted partner in the manufacturing industry.With the ever-increasing demand for high-quality, precision-engineered parts, the future of aluminum die casting looks brighter than ever. {Company Name} remains committed to staying at the forefront of this industry, continuously investing in the latest technologies and processes to meet the evolving needs of their clients.In conclusion, aluminum die casting has undoubtedly emerged as a game-changer in the manufacturing industry, and {Company Name} is leading the charge with its unparalleled expertise and dedication to excellence. As the industry continues to evolve, {Company Name} remains poised to deliver innovative solutions that will shape the future of manufacturing for years to come.
Guide to Insert Moulding: What You Need to Know
[Company Name] introduces new Insert Moulding technology for enhanced product quality[Company Name], a leading innovator in the manufacturing industry, has announced the introduction of a new Insert Moulding technology that is set to revolutionize the production of plastic and metal components. The new technology is designed to improve product quality and reduce production costs, providing a competitive edge in the market.Insert Moulding is a process in which a metal or plastic insert is placed into the mould before the material is injected, creating a strong and seamless bond between the insert and the surrounding material. This process is widely used in the manufacturing of electronics, automotive parts, medical devices, and consumer products.The introduction of this new technology by [Company Name] is a testament to their commitment to innovation and continuous improvement. With over three decades of experience in the industry, [Company Name] has a proven track record of delivering high-quality products and cutting-edge solutions to their customers.The new Insert Moulding technology is expected to bring several benefits to the company and its customers. By integrating inserts directly into the mould during the manufacturing process, [Company Name] will be able to produce components that are more durable, reliable, and cost-effective. This will in turn provide added value to their customers, as they will benefit from improved product performance and longevity.In addition to improving product quality, the new technology will also streamline the production process, reducing lead times and overall production costs. This will enable [Company Name] to offer competitive pricing and faster turnaround times to their customers, further enhancing their position in the market.“We are thrilled to introduce the new Insert Moulding technology to our production process,” said [Spokesperson Name], [Title] at [Company Name]. “This innovation represents a significant milestone for our company and our customers. We are confident that it will have a positive impact on our product quality, production efficiency, and overall customer satisfaction.”The introduction of Insert Moulding technology is also in line with [Company Name]’s commitment to sustainability and environmental responsibility. By streamlining the production process and reducing material waste, the company aims to minimize its environmental footprint and contribute to a more sustainable future.As a company that is always at the forefront of technological advancement, [Company Name] continues to invest in research and development to stay ahead of the curve. The introduction of Insert Moulding technology is just one example of their dedication to innovation and their constant pursuit of excellence in manufacturing.With the new technology now being integrated into their production process, [Company Name] is well-positioned to meet the evolving needs of their customers and drive growth in their respective markets. By offering enhanced product quality, improved production efficiency, and a lower environmental impact, the company is poised to set new standards in the manufacturing industry.As [Company Name] continues to expand its capabilities and offerings, the introduction of Insert Moulding technology marks a significant milestone in their journey towards becoming a leader in the industry. With a focus on innovation, quality, and customer satisfaction, the company is well-equipped to meet the demands of the market and deliver exceptional value to its customers.
Machined Custom PTFE Parts for Various Applications
Custom PTFE Parts Machined to PerfectionCustom PTFE (polytetrafluoroethylene) parts are in high demand across various industries due to their excellent chemical resistance, low friction, and high temperature performance. Companies are constantly in search of reliable manufacturers who can deliver precision machined PTFE parts that meet their specific requirements. One such company that has been making waves in the industry is [Company Name].[Company Name] is a leading manufacturer of custom PTFE parts, offering a wide range of machining capabilities to cater to the diverse needs of its customers. With a commitment to quality and precision, the company has established itself as a trusted partner for businesses looking for high-performance PTFE components.The company's state-of-the-art facility is equipped with advanced CNC machines and other cutting-edge technologies that enable it to deliver custom PTFE parts with tight tolerances and intricate geometries. From simple PTFE bushings to complex PTFE seals and gaskets, [Company Name] has the expertise and capabilities to machine a wide variety of PTFE parts to perfection.One of the key advantages of working with [Company Name] is its team of highly skilled engineers and technicians who have extensive experience in working with PTFE materials. They work closely with customers to understand their unique requirements and provide expert guidance to optimize the design and manufacturing processes, ensuring that the final parts meet the highest standards of quality and performance.In addition to its machining capabilities, [Company Name] also offers a range of secondary services such as precision welding, surface treatments, and custom packaging to provide a comprehensive solution for its customers' PTFE component needs. This end-to-end service approach has earned the company a reputation for delivering exceptional value and customer satisfaction.Recently, [Company Name] made significant investments in its infrastructure and capabilities to further enhance its machining capacity and efficiency. This includes the acquisition of new equipment and tools, as well as the implementation of advanced process controls to improve the overall quality and consistency of its custom PTFE parts.Furthermore, [Company Name] has also expanded its material options to include filled PTFE grades, such as glass-filled and carbon-filled PTFE, to meet the growing demand for specialized PTFE parts with enhanced mechanical properties. This strategic move has allowed the company to address a wider range of applications and industries, from automotive and aerospace to medical and chemical processing.The commitment to continuous improvement and innovation has positioned [Company Name] as a preferred supplier of custom PTFE parts for both small-scale businesses and large corporations. The company's dedication to meeting and exceeding customer expectations has resulted in numerous long-term partnerships and repeat business, testifying to the quality and reliability of its products and services.With a strong focus on precision, quality, and customer satisfaction, [Company Name] has demonstrated its ability to deliver custom PTFE parts machined to perfection. As the demand for high-performance PTFE components continues to grow, [Company Name] is well-positioned to uphold its reputation as a trusted industry leader in the machining of custom PTFE parts.
High-Quality Plastic Mold Components for Various Industries
Plastic Mold Components, a renowned and respected company in the industry, has made a name for itself by providing high-quality and innovative products for the plastic molding industry. With a strong emphasis on precision and reliability, the company has established itself as a leading supplier of mold components and tooling solutions for a wide range of applications.The company's extensive product line includes a variety of mold bases, mold components, hot runner systems, and other essential components for plastic injection molding. These products are designed to meet the demanding requirements of the industry and are built to deliver exceptional performance and durability.One of the key strengths of Plastic Mold Components is its commitment to innovation and continuous improvement. The company invests heavily in research and development to stay ahead of the curve and bring cutting-edge solutions to its customers. This dedication to innovation has enabled the company to develop a range of patented technologies and proprietary products that have set new standards in the industry.In addition to its focus on innovation, Plastic Mold Components is also dedicated to providing superior customer service and support. The company's team of skilled and experienced professionals is committed to working closely with customers to understand their specific needs and provide tailored solutions. Whether it's assisting with product selection, offering technical support, or providing onsite assistance, the team at Plastic Mold Components is always ready to go the extra mile to ensure customer satisfaction.Furthermore, the company's commitment to quality is evident in its rigorous quality control processes and adherence to industry standards. All products undergo strict testing and inspection to ensure they meet the highest standards for performance, reliability, and safety. This dedication to quality has earned Plastic Mold Components a reputation for excellence and reliability in the industry.Beyond its commitment to quality and innovation, Plastic Mold Components also places a strong emphasis on sustainability and environmental responsibility. The company is dedicated to minimizing its environmental footprint and continuously seeks ways to reduce waste, conserve resources, and operate in an environmentally friendly manner. This commitment to sustainability is not only reflected in the company's products but also in its operations and business practices.Looking ahead, Plastic Mold Components is poised for continued growth and success in the industry. With a strong foundation built on quality, innovation, and customer satisfaction, the company is well-positioned to meet the evolving needs of the plastic molding industry and continue to drive progress and excellence.In conclusion, Plastic Mold Components stands as a trusted partner and supplier for companies in the plastic molding industry. With a commitment to quality, innovation, and customer satisfaction, the company continues to deliver cutting-edge solutions and set new standards in the industry. As the company looks to the future, it remains dedicated to driving progress, sustainability, and success in the industry.
High-Quality and Efficient Short Run Injection Molding Services
Short Run Injection Molding, a leading provider of high-quality custom plastic injection molding, has been making waves in the industry with their innovative and efficient manufacturing processes. With a focus on short run production, the company has been able to consistently deliver top-notch products to their clients while maintaining a quick turnaround time.Founded in [year], Short Run Injection Molding has quickly risen to prominence in the industry. Their state-of-the-art facility is equipped with the latest in injection molding technology, allowing them to produce complex and intricate parts with precision and accuracy. The company's team of highly skilled engineers and technicians are dedicated to delivering the best possible solutions for their clients' unique needs.One of the key factors that set Short Run Injection Molding apart from their competitors is their ability to handle short run production effectively. Unlike traditional molding processes that require high-volume production to be cost-effective, Short Run Injection Molding specializes in producing small to medium batch sizes, making it an ideal solution for clients with limited production needs.The company's short run injection molding process is a highly efficient and cost-effective method of manufacturing plastic parts. By utilizing advanced mold-making techniques and cutting-edge materials, Short Run Injection Molding is able to produce parts that meet the strictest quality standards while minimizing waste and reducing production costs. This approach allows clients to benefit from fast production turnaround times and lower overall production costs, setting Short Run Injection Molding apart as a leader in the industry.In addition to their expertise in short run production, Short Run Injection Molding also offers a wide range of services to meet the diverse needs of their clients. From concept and design assistance to prototyping and full-scale production, the company is committed to providing comprehensive solutions to their clients' manufacturing challenges. Their dedication to quality and customer satisfaction has earned them a reputation as a trusted partner in the industry.Short Run Injection Molding also prides itself on its commitment to sustainability and environmental responsibility. The company utilizes advanced recycling and waste reduction techniques to minimize their environmental impact, ensuring that their manufacturing processes are as eco-friendly as possible. This dedication to sustainability not only benefits the environment but also allows Short Run Injection Molding to offer clients cost-effective and sustainable solutions for their plastic injection molding needs.With their innovative approach to short run production, commitment to quality, and dedication to sustainability, Short Run Injection Molding has established itself as a leader in the industry. The company's ability to consistently deliver high-quality products with quick turnaround times has made them a preferred choice for clients across a wide range of industries.Moving forward, Short Run Injection Molding remains focused on pushing the boundaries of injection molding technology and delivering even greater value to their clients. With a continued commitment to excellence and a passion for innovation, the company is poised to continue their rapid growth and solidify their position as a top provider of custom plastic injection molding solutions. As the industry evolves, Short Run Injection Molding will undoubtedly remain at the forefront, setting new standards for quality, efficiency, and sustainability in the manufacturing of plastic parts.
High-quality Electroplating Aluminum CNC Turning Parts
Manufacturing industry is undergoing a rapid transformation with the adoption of advanced technologies and innovative strategies to meet the growing demand for high-quality products. One company that is at the forefront of this revolution is {}, a leading manufacturer of precision machined parts and components.Based in {}, the company has built a solid reputation for delivering top-notch products and services to a wide range of industries, including automotive, aerospace, medical, and electronics. With a strong focus on quality and precision, {} has invested heavily in advanced manufacturing technologies to ensure that their customers receive the best possible solutions for their specific needs.One of the key capabilities that set {} apart from their competitors is their expertise in electroplating aluminum CNC turning parts. This specialized process involves coating aluminum parts with a thin layer of metal to enhance their surface properties and improve their performance in various applications. By leveraging their state-of-the-art CNC turning machines and extensive knowledge of electroplating techniques, {} is able to produce high-precision, high-performance aluminum parts that meet the stringent requirements of their customers.The electroplating process at {} begins with the preparation of the aluminum parts, which are carefully cleaned and pretreated to ensure optimal adhesion of the plating material. The parts are then placed in a specialized electroplating bath, where a thin layer of metal is deposited onto their surface through an electrochemical reaction. This metal coating not only improves the appearance of the parts but also provides enhanced corrosion resistance, wear resistance, and electrical conductivity.With their commitment to excellence, {} has perfected the art of electroplating aluminum CNC turning parts, offering their customers a range of benefits, including improved part longevity, reduced maintenance costs, and enhanced performance in demanding applications. Furthermore, the company's ability to tailor the plating process to meet the unique requirements of each customer's project underscores their dedication to providing customized solutions that exceed expectations.In addition to their expertise in electroplating, {} also offers a comprehensive range of CNC turning services, utilizing the latest computer-controlled machining centers to produce complex, high-precision parts with utmost efficiency. Their team of skilled machinists and engineers works closely with customers to understand their specific needs, providing valuable insights and technical expertise to optimize the design and manufacturing processes.The combination of advanced machining capabilities, in-depth material knowledge, and a commitment to quality makes {} a preferred partner for customers seeking reliable and cost-effective solutions for their precision machined part needs. Whether it's creating intricate components for aerospace applications or producing durable parts for the automotive industry, {} has the expertise and resources to deliver exceptional results.Looking ahead, {} is set to further expand their electroplating and CNC turning capabilities, leveraging emerging technologies and industry best practices to stay ahead of the curve. By continuing to invest in the latest equipment and talent, the company aims to strengthen its position as a leading provider of high-quality precision machined parts, meeting the evolving needs of its customers across industries.In conclusion, the electroplating aluminum CNC turning parts expertise of {} is a testament to their unwavering commitment to quality, innovation, and customer satisfaction. With a solid track record of delivering excellence, the company is poised to lead the way in the ever-evolving manufacturing landscape, setting new benchmarks for precision and performance in the industry.
High-Quality Precision Turning Components for CNC Machining Operations
CNC Precision Turning ComponentsIn the world of manufacturing, precision is key. Products must be made with exacting accuracy in order to meet the demands of modern consumers. This is where CNC precision turning components come into play. These components are an essential part of the manufacturing process, providing the precision and accuracy needed to create high-quality products.{Company Name} is a leading provider of CNC precision turning components. With years of experience and a dedication to quality, they have become a trusted name in the industry. Their components are used in a wide range of applications, including aerospace, automotive, and medical equipment. They are capable of producing components with tight tolerances and complex geometries, making them a valuable partner for companies looking to produce top-quality products.One of the key advantages of CNC precision turning components is their ability to produce parts with minimal human intervention. The CNC (Computer Numerical Control) technology used in these components allows for highly precise and consistent production, with minimal risk of error. This not only improves the quality of the products, but also reduces the time and cost of production.{Company Name}'s CNC precision turning components are made using state-of-the-art equipment and the latest manufacturing techniques. This allows them to produce components with exceptional accuracy and reliability. Their team of skilled engineers and technicians work closely with clients to develop custom solutions for their specific needs, ensuring that the final product meets their exact specifications.In addition to their precision and reliability, {Company Name}'s CNC precision turning components are also known for their versatility. They can be used to produce a wide range of parts and components, including shafts, valves, fittings, and much more. This flexibility makes them a valuable resource for companies looking to streamline their manufacturing processes and improve their overall efficiency.The demand for CNC precision turning components continues to grow, as manufacturers seek to improve the quality and performance of their products. As a result, {Company Name} is constantly expanding and upgrading their capabilities to meet the needs of their clients. They are committed to staying at the forefront of CNC technology, ensuring that their components are always at the cutting edge of the industry.With their dedication to quality, precision, and innovation, {Company Name} has solidified their position as a leader in the field of CNC precision turning components. Their components are trusted by companies around the world to produce high-quality products with unmatched accuracy and reliability. As the demand for precision manufacturing continues to grow, {Company Name} is well-positioned to meet the needs of their clients and continue to push the boundaries of what is possible in modern manufacturing.In conclusion, CNC precision turning components are an essential part of modern manufacturing, allowing companies to produce high-quality products with exceptional precision and reliability. {Company Name} is a trusted provider of these components, with a proven track record of delivering top-quality solutions to their clients. Their dedication to innovation and quality makes them a valuable partner for companies looking to take their manufacturing processes to the next level.
High-Quality TPE Injection Molding Services for Your Business
TPE Injection Molding Industry Shows Strong Growth PotentialTPE injection molding is a rapidly growing industry that is gaining significant attention from manufacturers and consumers alike. Thermoplastic elastomers (TPE) offer a unique set of properties that make them an ideal choice for a wide range of applications, from automotive components and consumer products to medical devices and industrial equipment. With the increasing demand for high-performance, lightweight, and durable materials, the TPE injection molding market is expected to experience continued growth in the coming years.One company at the forefront of the TPE injection molding industry is {}. Founded in {}, the company has established itself as a leading global manufacturer of TPE materials and injection molding solutions. With a strong focus on innovation, quality, and customer satisfaction, {} has quickly become a preferred partner for businesses looking to leverage the benefits of TPE injection molding in their product development.{} offers a comprehensive range of TPE materials, including thermoplastic vulcanizates (TPVs), thermoplastic polyurethanes (TPUs), and styrenic block copolymers (SBCs). These materials are known for their excellent elasticity, flexibility, weather resistance, and high-performance characteristics, making them suitable for a wide variety of applications. From soft-touch grips and seals to flexible gaskets and impact-resistant parts, {}'s TPE materials have been widely adopted across industries for their versatility and reliability.In addition to its extensive TPE material portfolio, {} has also developed a range of advanced injection molding technologies to meet the evolving needs of its customers. The company's state-of-the-art injection molding equipment and expertise enable it to produce complex TPE components with precision and efficiency. Whether it's overmolding, insert molding, or multi-material molding, {} has the capabilities to deliver custom TPE solutions that meet the specific requirements of each application.One of the key advantages of TPE injection molding is its ability to reduce manufacturing costs and lead times, while offering design flexibility and part integration opportunities. By leveraging {}'s expertise in TPE injection molding, businesses can achieve higher production efficiency, lower tooling costs, and faster time-to-market for their products. This has made TPE injection molding an attractive option for companies looking to optimize their manufacturing processes and gain a competitive edge in their respective markets.With a strong commitment to sustainability and environmental responsibility, {} also offers eco-friendly TPE materials that are recyclable and compliant with industry regulations. By choosing {} as their TPE injection molding partner, businesses can align with sustainable practices and contribute to a more circular economy by reducing their carbon footprint and waste generation.As the TPE injection molding industry continues to evolve, {} remains dedicated to driving innovation and delivering cutting-edge solutions that address the diverse needs of its customers. With a focus on continuous improvement and customer-centric approach, the company is well-positioned to capitalize on the growing demand for TPE materials and injection molding services across various industries.Looking ahead, the future of TPE injection molding appears promising, with advancements in material science, process technology, and end-use applications. As businesses seek to enhance product performance, aesthetics, and sustainability, TPE injection molding is expected to play a pivotal role in shaping the next generation of innovative products.In conclusion, the TPE injection molding industry, led by companies like {}, is poised for substantial growth in the years to come. With its extensive expertise, diverse material portfolio, and advanced manufacturing capabilities, {} is well-equipped to meet the evolving needs of its customers and drive the widespread adoption of TPE injection molding across industries. As demand for high-performance, sustainable, and cost-effective solutions continues to rise, TPE injection molding is set to revolutionize the way manufacturers design and produce their products.