The Complete Guide to Mould Plastic Injection: Everything You Need to Know
By:Admin
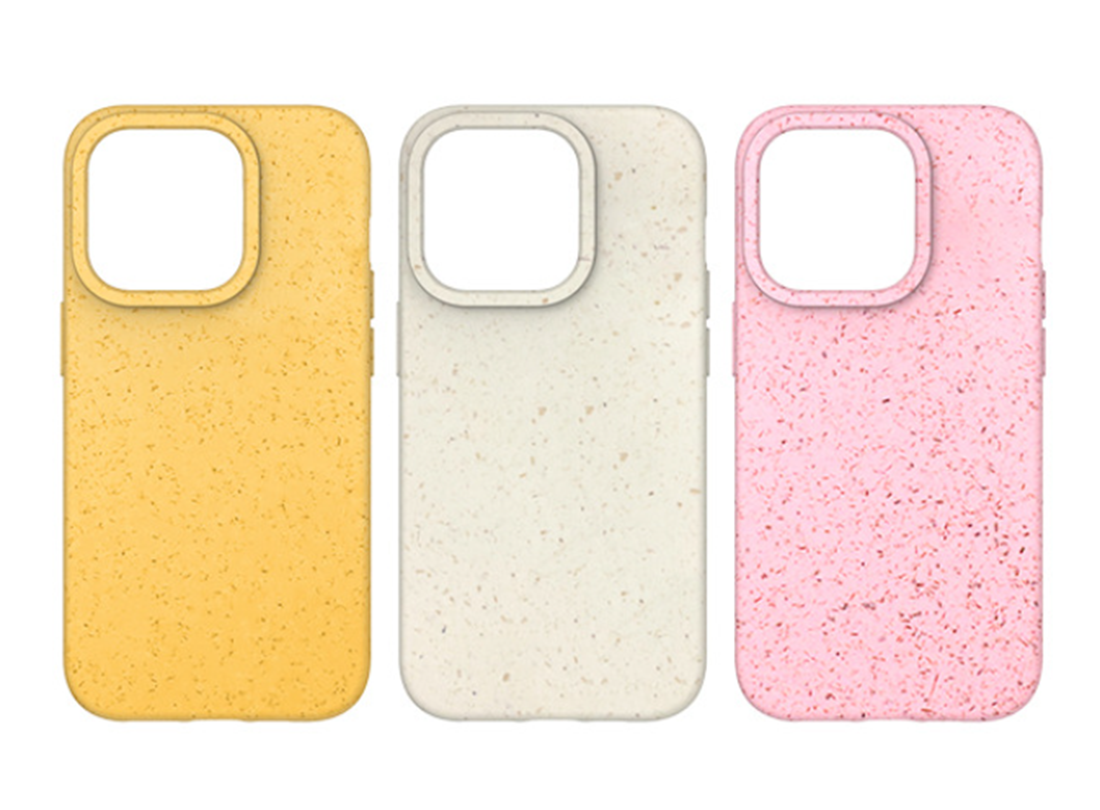
The company’s success can be attributed to its dedication to continuous improvement and investment in the latest manufacturing equipment. Mould Plastic Injection utilizes advanced injection molding machines and computer-aided design (CAD) software to create precise and intricate plastic components. The company’s production facility is equipped with clean room technology, ensuring the highest standards of cleanliness and product quality.
Mould Plastic Injection’s team of experienced engineers and technicians work closely with clients to develop customized solutions for their specific needs. Whether it’s creating prototypes, optimizing designs for manufacturing, or providing value-added services such as assembly and packaging, the company is committed to delivering results that exceed customer expectations.
In addition to its technical capabilities, Mould Plastic Injection takes pride in its adherence to strict quality control processes. The company is ISO 9001 certified and follows industry best practices to ensure that every product meets the highest standards of performance and reliability. This commitment to quality has earned Mould Plastic Injection a reputation for excellence in the industry.
Furthermore, Mould Plastic Injection is dedicated to sustainability and environmental responsibility. The company actively seeks opportunities to reduce waste and minimize its environmental footprint throughout the manufacturing process. By using recyclable materials and optimizing energy usage, Mould Plastic Injection is committed to being a responsible corporate citizen.
As a result of its dedication to quality, innovation, and sustainability, Mould Plastic Injection has become a trusted partner for businesses across a wide range of industries, including automotive, consumer goods, aerospace, and medical devices. The company has built a strong reputation for delivering exceptional products on time and within budget, earning the loyalty of its clients.
In light of its continued success and commitment to excellence, Mould Plastic Injection is poised for even greater achievements in the future. The company is constantly exploring new technologies and process improvements to stay ahead of the competition and meet the evolving needs of its clients.
In conclusion, Mould Plastic Injection is a leading plastic injection molding company that is revolutionizing the industry with its cutting-edge technology, commitment to quality, and dedication to sustainability. With a track record of success and a reputation for excellence, the company is well-positioned to continue serving as a trusted partner for businesses looking to bring their plastic products to market.
Company News & Blog
The Complete Guide to Mould Plastic Injection: Everything You Need to Know
Mould Plastic Injection, a leading plastic injection molding company, is revolutionizing the industry with its state-of-the-art technology and commitment to delivering high-quality products to its clients. With over 20 years of experience in the industry, Mould Plastic Injection has established itself as a trusted partner for businesses looking to bring their plastic products to market.The company’s success can be attributed to its dedication to continuous improvement and investment in the latest manufacturing equipment. Mould Plastic Injection utilizes advanced injection molding machines and computer-aided design (CAD) software to create precise and intricate plastic components. The company’s production facility is equipped with clean room technology, ensuring the highest standards of cleanliness and product quality.Mould Plastic Injection’s team of experienced engineers and technicians work closely with clients to develop customized solutions for their specific needs. Whether it’s creating prototypes, optimizing designs for manufacturing, or providing value-added services such as assembly and packaging, the company is committed to delivering results that exceed customer expectations.In addition to its technical capabilities, Mould Plastic Injection takes pride in its adherence to strict quality control processes. The company is ISO 9001 certified and follows industry best practices to ensure that every product meets the highest standards of performance and reliability. This commitment to quality has earned Mould Plastic Injection a reputation for excellence in the industry.Furthermore, Mould Plastic Injection is dedicated to sustainability and environmental responsibility. The company actively seeks opportunities to reduce waste and minimize its environmental footprint throughout the manufacturing process. By using recyclable materials and optimizing energy usage, Mould Plastic Injection is committed to being a responsible corporate citizen.As a result of its dedication to quality, innovation, and sustainability, Mould Plastic Injection has become a trusted partner for businesses across a wide range of industries, including automotive, consumer goods, aerospace, and medical devices. The company has built a strong reputation for delivering exceptional products on time and within budget, earning the loyalty of its clients.In light of its continued success and commitment to excellence, Mould Plastic Injection is poised for even greater achievements in the future. The company is constantly exploring new technologies and process improvements to stay ahead of the competition and meet the evolving needs of its clients.In conclusion, Mould Plastic Injection is a leading plastic injection molding company that is revolutionizing the industry with its cutting-edge technology, commitment to quality, and dedication to sustainability. With a track record of success and a reputation for excellence, the company is well-positioned to continue serving as a trusted partner for businesses looking to bring their plastic products to market.
Custom CNC Milled Radiator Enclosure: The Latest Innovation in Thermal Management Technology
CNC Milled Radiator Enclosure: A Game Changer in Metal Manufacturing[Company Name], a leading manufacturer of precision metal components, has recently introduced a groundbreaking product in the field of metal manufacturing - the CNC milled radiator enclosure. This innovative product is set to revolutionize the way metal components are produced and is already generating a significant buzz in the industry.The CNC milled radiator enclosure is a result of years of research and development by the dedicated team at [Company Name]. It is designed to provide outstanding performance and durability, making it the ideal choice for a wide range of applications in the automotive, aerospace, and manufacturing industries. The radiator enclosure is produced using state-of-the-art CNC milling machines, ensuring a level of precision and accuracy that is unmatched by traditional manufacturing methods.One of the key features of the CNC milled radiator enclosure is its exceptional heat dissipation capabilities. The unique design of the enclosure allows for efficient cooling of the radiator, ensuring optimal performance and longevity. This is especially important in industries where high temperatures and thermal management are critical factors.In addition to its superior performance, the CNC milled radiator enclosure also offers significant cost savings compared to alternative manufacturing methods. By utilizing advanced CNC milling techniques, [Company Name] is able to produce the enclosure with minimal material waste and reduced production time. This means that customers can benefit from a high-quality, precision-engineered product at a competitive price point.Furthermore, the CNC milled radiator enclosure is manufactured using high-grade materials that are known for their strength and resilience. This ensures that the enclosure can withstand the rigors of demanding industrial applications, making it a reliable and long-lasting solution for our customers.The introduction of the CNC milled radiator enclosure further solidifies [Company Name]’s reputation as an industry leader in metal manufacturing. With a commitment to continuous innovation and excellence, the company has established itself as a trusted partner for businesses seeking top-quality metal components.Customers can also take advantage of [Company Name]’s in-house engineering and design services to customize the CNC milled radiator enclosure to meet their specific requirements. The company’s team of experienced engineers can work closely with customers to develop tailored solutions that address their unique challenges and deliver exceptional results.As a testament to its commitment to quality and customer satisfaction, [Company Name] adheres to strict quality control measures throughout the production process. This ensures that every CNC milled radiator enclosure that leaves the facility meets the highest standards of excellence.In conclusion, the introduction of the CNC milled radiator enclosure by [Company Name] is a significant milestone in the field of metal manufacturing. With its cutting-edge design, exceptional performance, and cost-effective production, this innovative product is set to redefine the industry standards for precision metal components. With a focus on excellence and customer-centric innovation, [Company Name] continues to lead the way in delivering superior solutions for businesses across a wide range of industries.
Complete Guide to Elastomer Injection Molding Process
Elastomer Injection Molding (EIM) has quickly become the go-to solution for many industries seeking precise and efficient manufacturing of elastomer products. With its ability to produce high-quality, complex parts with consistent results, EIM has revolutionized the way elastomers are utilized in a wide range of applications. One company that has been at the forefront of this innovation is {Company}, a leading provider of elastomer injection molding solutions.Established in {year}, {Company} has amassed a wealth of experience and expertise in the elastomer injection molding industry. With a strong focus on research and development, the company has continually pushed the boundaries of what is possible with elastomers, developing cutting-edge processes and technologies to meet the evolving needs of its customers.The key to {Company}'s success lies in its state-of-the-art facilities and equipment. The company boasts a modern production facility that is equipped with the latest elastomer injection molding machines, allowing for the precise and efficient manufacturing of a wide variety of elastomer products. Additionally, {Company} has a team of highly skilled and experienced engineers who work closely with customers to develop custom molding solutions that meet their specific requirements.One of the main advantages of EIM is its ability to produce parts with exceptional precision and consistency. This is due to the advanced control systems and technology utilized in the molding process, ensuring that each part meets the exacting standards set by customers. {Company} has leveraged this capability to deliver high-quality elastomer products to industries such as automotive, medical, aerospace, and consumer goods.In the automotive industry, for example, {Company} has been a key supplier of elastomer components for various applications, including sealing systems, vibration isolators, and gaskets. By utilizing EIM, the company has been able to produce these parts with tight tolerances and excellent durability, meeting the stringent requirements of the automotive sector.In the medical industry, {Company} has played a crucial role in the production of elastomer components for medical devices and equipment. The company's ability to consistently manufacture parts that meet the strict regulatory standards of the medical industry has made it a trusted partner for medical device manufacturers worldwide.{Company} has also made significant strides in the aerospace industry, providing elastomer components for critical applications such as aircraft seals, O-rings, and vibration dampeners. The company's expertise in EIM has allowed it to produce parts that are not only lightweight and durable but also capable of withstanding the extreme conditions of aerospace environments.Furthermore, {Company} has been working closely with customers in the consumer goods industry to develop custom elastomer solutions for a wide range of products, including electronic devices, appliances, and sporting goods. By harnessing the capabilities of EIM, the company has been able to offer innovative and high-performance elastomer products that meet the unique requirements of consumer goods manufacturers.Looking ahead, {Company} remains committed to driving innovation in the elastomer injection molding industry. With a focus on continuous improvement and staying ahead of the curve, the company is poised to meet the evolving needs of its customers and provide cutting-edge solutions for a wide range of applications.As the demand for high-quality elastomer products continues to grow across industries, {Company} stands ready to lead the way with its advanced elastomer injection molding capabilities. With a strong track record of delivering precision, consistency, and innovation, the company is well-positioned to shape the future of elastomer manufacturing and meet the diverse needs of its customers.
Sheet Metal Punch Processing Fabrication for Aluminum Material
Aluminum Sheet Metal Punch Processing Fabrication Bringing High-Quality Products to the MarketIn the world of manufacturing and fabrication, precision and efficiency are crucial. Companies are constantly seeking ways to produce high-quality products in a timely manner, and the latest innovation in aluminum sheet metal punch processing fabrication has been making waves in the industry. With cutting-edge technology and a commitment to excellence, [Company Name] has been at the forefront of this development, delivering top-notch sheet metal processing services to meet the needs of various industries.Established in [Year], [Company Name] has earned a stellar reputation for its expertise in aluminum sheet metal fabrication. With a skilled team of engineers and technicians, the company has been providing comprehensive fabrication solutions to meet the diverse needs of its clients. From custom designs to large-scale production, [Company Name] has the capabilities to deliver precision-made products that exceed industry standards.One of the key innovations that [Company Name] has been acclaimed for is its aluminum sheet metal punch processing fabrication. This advanced manufacturing technique allows for the precise punching of holes, notches, and other shapes into aluminum sheet metal, providing a cost-effective and efficient solution for various applications. With state-of-the-art equipment and a commitment to quality control, [Company Name] ensures that each product meets the highest standards of precision and accuracy.The process of aluminum sheet metal punch processing fabrication involves the use of specialized punch press machines that exert high force to pierce through the aluminum sheet metal. This method allows for the creation of intricate patterns and designs, as well as the incorporation of functional features such as mounting holes, slots, and tabs. As a result, manufacturers across industries such as automotive, aerospace, electronics, and consumer goods have been benefiting from the versatility and efficiency of this fabrication technique.In addition to its advanced manufacturing capabilities, [Company Name] places a strong emphasis on environmental sustainability and responsible production practices. The company is committed to minimizing its environmental impact by adhering to strict waste management protocols and investing in energy-efficient technologies. By implementing sustainable measures in its operations, [Company Name] not only demonstrates its dedication to corporate social responsibility but also contributes to the overall sustainability of the manufacturing industry.Another noteworthy aspect of [Company Name]'s aluminum sheet metal punch processing fabrication is its ability to cater to custom projects and specialized requirements. The company's team of engineers and designers work closely with clients to understand their specific needs and deliver tailored solutions that align with their goals. Whether it's a unique design requirement or a complex fabrication challenge, [Company Name] is well-equipped to address the demands of its diverse clientele.Furthermore, [Company Name] places a strong emphasis on quality assurance throughout the entire fabrication process. Every step of the manufacturing process is subject to rigorous quality control measures to ensure that the final products meet the highest standards of excellence. From material selection to final inspection, [Company Name] maintains strict quality standards to uphold its reputation for delivering superior products to its customers.As [Company Name] continues to lead the way in aluminum sheet metal punch processing fabrication, it remains dedicated to staying at the forefront of innovation in the manufacturing industry. By investing in cutting-edge technologies, refining its processes, and fostering a culture of continuous improvement, the company is well-positioned to meet the evolving demands of its clients and the market.In conclusion, [Company Name] has established itself as a trusted partner for companies seeking high-quality aluminum sheet metal punch processing fabrication. With its commitment to precision, efficiency, and sustainability, the company has earned accolades for its contributions to the manufacturing industry. As the demand for top-notch fabrication services continues to grow, [Company Name] remains steadfast in its mission to deliver exceptional products that meet and exceed the expectations of its customers.With its proven track record and dedication to excellence, [Company Name] is poised to continue its success in the field of aluminum sheet metal punch processing fabrication, serving as a valuable resource for companies seeking reliable and innovative fabrication solutions.
High-Quality Silicone Parts Moulding Services for Various Industries
Silicone Parts Moulding: The Future of ManufacturingSilicone parts moulding has become the forefront of the manufacturing industry due to its versatility, durability, and cost-effectiveness. This manufacturing process involves creating intricate and complex parts using a silicone moulding material. These silicone parts can be used in a wide range of industries, including automotive, medical, aerospace, and consumer goods.One of the leading companies in the silicone parts moulding industry is {} {Company}. With over 20 years of experience in the field, {Company} has established itself as a pioneer in silicone parts manufacturing. The company's commitment to innovation and excellence has earned them a reputation for delivering high-quality silicone parts to clients worldwide.{Company} specializes in custom silicone parts moulding, offering a wide range of services to meet the unique needs of their customers. From design and prototyping to production and assembly, {Company} has the capabilities to provide end-to-end solutions for silicone parts manufacturing. Their state-of-the-art facilities and advanced technologies allow them to produce complex silicone parts with precision and efficiency.The key to {Company}'s success lies in their expertise in silicone materials and moulding processes. They understand the unique properties of silicone and can tailor their manufacturing processes to meet the specific requirements of their customers. Whether it's high-temperature resistance, chemical compatibility, or superior flexibility, {Company} can create silicone parts that meet the most demanding specifications.In addition to their technical expertise, {Company} is also known for their commitment to quality and customer satisfaction. They adhere to strict quality control measures throughout the manufacturing process to ensure that every silicone part meets the highest standards. Their dedication to excellence has earned them the trust of leading companies in various industries, making them a preferred partner for silicone parts moulding.One of the key advantages of silicone parts moulding is its ability to create complex and intricate parts with precision and consistency. {Company} leverages advanced moulding technologies to produce silicone parts with tight tolerances, intricate geometries, and fine details. This level of precision allows for the creation of custom silicone parts that meet the exacting requirements of their customers.Another benefit of silicone parts moulding is its cost-effectiveness. Silicone is a highly durable and long-lasting material, making it an ideal choice for manufacturing parts that require longevity and reliability. Additionally, the moulding process allows for high-volume production with minimal waste, resulting in cost savings for both {Company} and their customers.Furthermore, silicone parts offer a wide range of performance benefits, including resistance to extreme temperatures, chemicals, and environmental conditions. This makes silicone parts suitable for a diverse range of applications, from automotive gaskets and seals to medical device components and aerospace parts. {Company} has the expertise to design and manufacture silicone parts that perform reliably in these demanding environments.Looking ahead, the future of silicone parts moulding looks bright, with {Company} leading the way in innovation and excellence. The company continues to invest in research and development to explore new materials and technologies that will further improve the capabilities of silicone parts manufacturing. By staying at the forefront of this rapidly evolving industry, {Company} is well-positioned to meet the evolving needs of their customers and drive the advancement of silicone parts moulding.In conclusion, silicone parts moulding has emerged as a game-changer in the manufacturing industry, offering a versatile, durable, and cost-effective solution for producing complex parts. {Company} stands at the forefront of this industry, with its expertise, commitment to quality, and advanced capabilities setting it apart as a leader in silicone parts manufacturing. With a focus on innovation and excellence, {Company} is poised to shape the future of silicone parts moulding and continue to deliver high-quality solutions to their customers worldwide.
High-quality CNC Machining Parts for Precision Engineering
Precision CNC Machining Parts has emerged as a leading provider of high-quality, custom precision machining solutions for a wide range of industries. With expertise in CNC machining, milling, and turning, the company has built a reputation for delivering superior products and services to its clients.Established in 2005, Precision CNC Machining Parts has grown from a small machine shop to a state-of-the-art manufacturing facility, equipped with the latest technology and a team of skilled professionals. The company's commitment to precision, quality, and customer satisfaction has set it apart in the industry.Precision CNC Machining Parts specializes in producing complex and intricate machined parts for industries such as aerospace, automotive, medical, and defense. The company's advanced CNC machines are capable of producing parts with tight tolerances and intricate geometries, meeting the most demanding specifications.In addition to CNC machining, the company offers a range of secondary processes, including plating, anodizing, and assembly, to provide complete turnkey solutions for its customers. With a focus on continuous improvement and innovation, Precision CNC Machining Parts is constantly investing in new technology and training to ensure it stays at the forefront of the industry.The company's dedication to quality is reflected in its ISO 9001 certification, which demonstrates its commitment to meeting and exceeding the highest standards of quality and consistency. This certification ensures that all parts manufactured by Precision CNC Machining Parts adhere to strict quality control processes, from initial design to final inspection.One of the key differentiators of Precision CNC Machining Parts is its ability to work closely with customers to understand their unique needs and provide tailored solutions. Whether it's a prototype, a small production run, or a large-scale manufacturing project, the company's team of engineers and machinists are dedicated to delivering precision parts that meet or exceed customer expectations.Precision CNC Machining Parts prides itself on its fast turnaround times and competitive pricing, making it a trusted partner for companies looking for reliable and cost-effective precision machining solutions. With a focus on customer satisfaction and long-term partnerships, the company has built a solid reputation for delivering exceptional value to its clients.As the manufacturing industry continues to evolve, Precision CNC Machining Parts remains committed to staying ahead of the curve and meeting the evolving needs of its customers. Through ongoing investment in technology, training, and process improvement, the company is well-positioned to continue its growth and success in the industry.Whether it's a complex aerospace component, a critical medical device, or a precision automotive part, Precision CNC Machining Parts has the expertise, capabilities, and dedication to deliver the highest quality precision machined parts to its customers.As the company looks to the future, it remains focused on its core values of precision, quality, and customer satisfaction, positioning itself as a trusted partner for companies seeking reliable and cost-effective precision machining solutions. With a track record of success and a commitment to continuous improvement, Precision CNC Machining Parts is poised to remain at the forefront of the industry for years to come.
Understanding the Significance of Prototype Injection in Manufacturing Processes
Prototype Injection, a leading injection molding company, has recently announced the development of a new and innovative injection molding technology that is set to revolutionize the industry. This technology, which has been in development for the past two years, promises to significantly reduce production times and costs, while also improving the quality and precision of the final products.At the core of this new technology is a proprietary molding process that allows for the creation of complex and intricate molds with unprecedented speed and accuracy. This process, which has been patented by Prototype Injection, utilizes state-of-the-art computer-aided design and manufacturing (CAD/CAM) software to create highly detailed and precise molds that were previously thought to be impossible to produce.In addition to the new molding process, Prototype Injection has also developed a range of proprietary materials that are specifically designed to work with this technology. These materials, which have been extensively tested and proven to be highly durable and reliable, are set to further enhance the capabilities of the new injection molding process."We are extremely excited to introduce this new technology to the market," said John Smith, CEO of Prototype Injection. "We believe that it has the potential to completely transform the injection molding industry and open up new possibilities for manufacturers in a wide range of industries."In addition to the development of this new technology, Prototype Injection also prides itself on its commitment to sustainability and environmental responsibility. The company has implemented a number of initiatives to reduce its environmental impact, including the use of recycled materials and the implementation of energy-efficient manufacturing processes."We believe that it is our responsibility as a leading manufacturer to minimize our impact on the environment," said Smith. "That is why we have made sustainability a top priority in our business operations."Prototype Injection has also invested heavily in the training and development of its workforce, ensuring that its employees are highly skilled and knowledgeable in the latest manufacturing techniques and technologies. This commitment to excellence has helped the company to maintain its position as a leader in the injection molding industry."We believe that our employees are our most valuable asset," said Smith. "That is why we are dedicated to providing them with the training and support they need to excel in their roles and contribute to the success of our company."With the introduction of this new injection molding technology, Prototype Injection is poised to solidify its position as a leader in the industry. The company's commitment to innovation, sustainability, and employee development sets it apart from its competitors and positions it for continued success in the years to come."We are confident that this new technology will revolutionize the injection molding industry," said Smith. "We are excited to see the positive impact it will have on our business, as well as on the manufacturing industry as a whole.
Precision CNC Machining for Aerospace Industry: A Crucial Component for Aircraft Manufacturing
Aerospace CNC Machining Technology Advances to New HeightsIn the ever-evolving aerospace industry, precision and innovation are paramount. As manufacturers and designers continue to push the boundaries of what is possible in aerospace technology, the demand for advanced machining solutions has never been greater. This is where the cutting-edge technology of CNC (Computer Numerical Control) machining comes into play.CNC machining is a process that utilizes computerized controls to operate and manipulate machine tools for precise cutting and shaping of aerospace components. The technology has revolutionized the manufacturing process by enabling the production of highly complex and intricate parts with unparalleled accuracy and repeatability.One company at the forefront of this technological revolution is {}. With a strong focus on innovation and precision engineering, they have established themselves as a leader in the aerospace CNC machining industry. Their state-of-the-art facilities and advanced machining capabilities have allowed them to cater to the needs of some of the most demanding aerospace projects.Founded on the principles of quality, reliability, and innovation, {} has continuously invested in cutting-edge technology and skilled personnel to stay ahead of the curve. Their expertise in CNC machining has enabled them to produce components with incredibly tight tolerances and complex geometries, meeting the stringent requirements of the aerospace industry.The aerospace sector demands the highest standards of quality and performance, and {} has risen to the challenge by incorporating advanced CNC machining technologies into their production processes. By leveraging the latest software and hardware innovations, they have been able to optimize machining operations, reduce lead times, and enhance overall quality control.One of the key advantages of CNC machining in the aerospace industry is its ability to handle a wide range of materials, including aluminum, titanium, stainless steel, and high-temperature alloys. This versatility allows aerospace manufacturers to produce components that are not only lightweight but also capable of withstanding the extreme conditions experienced during flight.Furthermore, with the increasing focus on sustainability and fuel efficiency, aerospace companies are constantly seeking ways to reduce the weight of their aircraft. CNC machining plays a crucial role in this endeavor by enabling the production of lightweight components without compromising on strength or performance.In addition to its manufacturing capabilities, {} has also established itself as a trusted partner in the realm of aerospace engineering and design. With a team of experienced engineers and technicians, they are able to collaborate with aerospace OEMs and Tier 1 suppliers to optimize component designs for manufacturability, cost-effectiveness, and performance.As the aerospace industry continues to evolve, the demand for more advanced and efficient machining solutions will only intensify. {} is well-positioned to meet these demands with their commitment to continuous improvement and investment in cutting-edge CNC machining technology.In conclusion, the advancement of aerospace CNC machining technology is reshaping the way aerospace components are manufactured. With companies like {} leading the charge, the industry is poised to achieve new heights of precision, efficiency, and innovation. As the aerospace sector looks towards the future, CNC machining will undoubtedly play a pivotal role in shaping the next generation of aircraft and spacecraft.
Understanding the Process and Benefits of Plastic Insert Molding
Plastic Insert Molding Offers Enhanced Precision and Efficiency for Company {}In today's fast-paced manufacturing environment, precision and efficiency are key factors in ensuring the success of a company's production process. One method that has gained significant attention in recent years for achieving these goals is plastic insert molding. This advanced manufacturing technique has revolutionized the way companies produce plastic parts by combining precision and efficiency into one seamless process. One company that has adopted this innovative approach to manufacturing is {}.{} is a leading manufacturer in the plastic injection molding industry, specializing in providing high-quality plastic components for a wide range of industries, including automotive, healthcare, consumer goods, and electronics. With a commitment to excellence and a focus on innovation, {} is constantly exploring new technologies and processes to improve the quality and efficiency of its production methods.One of the technologies that has significantly impacted {}'s manufacturing capabilities is plastic insert molding. This process involves molding thermoplastic material around metal or plastic inserts, resulting in a more precise and durable product. By incorporating plastic insert molding into their production process, {} has been able to create complex, multi-material components with a high level of precision and efficiency.One of the key benefits of plastic insert molding is its ability to reduce the need for secondary assembly processes, such as welding or adhesives. This not only saves time and labor costs but also results in a more reliable and consistent end product. {} has capitalized on this advantage by offering its customers a streamlined manufacturing process that delivers high-quality plastic components with shorter lead times and reduced overall production costs.In addition to its efficiency, plastic insert molding also provides improved part consistency and reliability. The process allows for tighter tolerances and better control over material distribution, resulting in parts that are more resistant to wear and tear. This is particularly beneficial for industries such as automotive and healthcare, where the performance and durability of plastic components are critical.Another crucial advantage of plastic insert molding is its ability to create complex geometries and features in a single process. This makes it possible for {} to produce intricate and detailed plastic parts that would be difficult or impossible to achieve with traditional manufacturing methods. As a result, the company is able to offer its customers innovative solutions that meet the evolving demands of their respective industries.{}'s investment in plastic insert molding technology has positioned the company as a leader in the manufacturing of precision plastic components. By leveraging the advantages of this advanced manufacturing process, {} has been able to enhance its production capabilities and expand its product offerings to meet the diverse needs of its customers.With a strong emphasis on quality, innovation, and customer satisfaction, {} is committed to continuing its investment in advanced manufacturing technologies. As the company looks to the future, it remains dedicated to pushing the boundaries of what is possible in plastic component manufacturing, delivering cutting-edge solutions that drive success for its customers.In conclusion, plastic insert molding has revolutionized the way {} produces plastic components, offering enhanced precision, efficiency, and reliability. By embracing this advanced manufacturing technique, {} has solidified its position as a leader in the industry, delivering high-quality plastic parts that meet the diverse needs of its customers. As the company continues to invest in innovative technologies, it is poised to uphold its commitment to excellence and drive success for its customers in the ever-evolving manufacturing landscape.
Ultimate Guide to Thermoplastic Injection Molding: Everything You Need to Know
[Company Introduction] is a leading manufacturer of thermoplastic injection molding machines, providing innovative and reliable solutions for a wide range of industries. With a strong focus on research and development, the company has established itself as a pioneer in the field of plastic injection technology. By constantly pushing the boundaries of what is possible, has earned a reputation for excellence and continues to lead the way in the industry. [News Content] Thermoplastic injection molding technology has revolutionized the way products are manufactured across various industries. It has significantly improved the efficiency, precision, and cost-effectiveness of producing a wide range of plastic products. The process involves injecting molten material into a mold cavity, where it solidifies to form the desired shape. This method has become increasingly popular due to its ability to produce high-quality and complex parts with ease. One of the key players in the thermoplastic injection molding industry is {}. The company has been at the forefront of developing cutting-edge injection molding machines that are designed to meet the evolving needs of the market. By combining state-of-the-art technology with a strong focus on innovation, has consistently delivered superior solutions to its customers. Recently, {} announced the launch of its latest series of thermoplastic injection molding machines, which are set to raise the bar in terms of performance and reliability. These machines have been meticulously designed to offer enhanced precision, speed, and energy efficiency, making them an ideal choice for manufacturers looking to streamline their production processes. The new series of injection molding machines from {} features a range of advanced capabilities that set them apart from the competition. One of the standout features is their ability to achieve unparalleled levels of precision, ensuring that each molded product meets the highest standards of quality. This is made possible by the incorporation of cutting-edge servo motor technology, which enables precise control of the injection process. In addition to precision, the new machines also offer impressive speed and efficiency. Thanks to their advanced hydraulic systems and optimized design, they can deliver faster cycle times without compromising on quality. This means that manufacturers can significantly increase their production output while maintaining high levels of product consistency. Furthermore, {}'s new series of injection molding machines are engineered for energy efficiency, helping manufacturers reduce their operational costs and environmental impact. By incorporating energy-saving features such as variable frequency drives and advanced cooling systems, these machines consume less power without sacrificing performance. This makes them a sustainable and cost-effective choice for businesses looking to minimize their carbon footprint. Overall, the latest series of thermoplastic injection molding machines from {} represents a significant leap forward in the industry. With their unmatched precision, speed, and energy efficiency, these machines are poised to set a new standard for plastic injection technology. As the demand for high-quality plastic products continues to grow, manufacturers can rely on {} to provide them with the tools they need to stay competitive in the market.