Advanced 4 Axis Machining: What You Need to Know
By:Admin
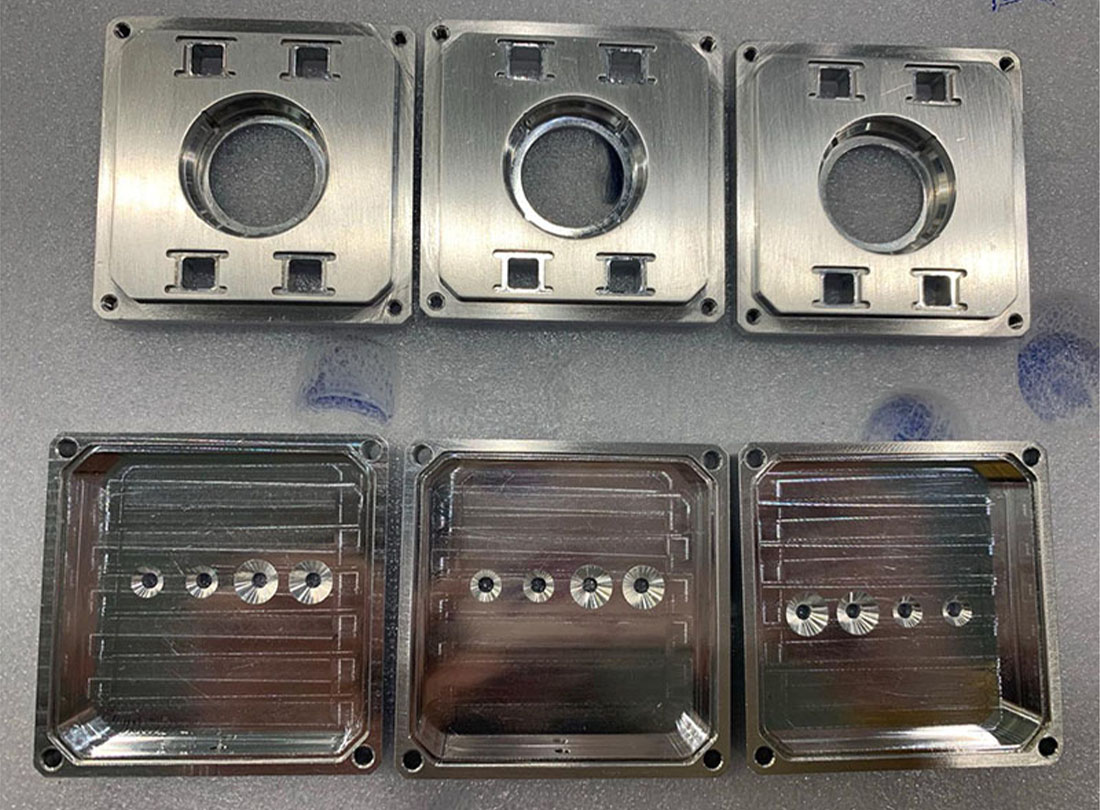
In the ever-evolving world of manufacturing and precision engineering, staying ahead of the curve is crucial for any company looking to maintain a competitive edge. That's why {Company Name}, a leader in the manufacturing industry, has recently announced the introduction of advanced 4 axis machining technology to their production line.
This new technology allows {Company Name} to offer an even greater level of precision and efficiency in their machining processes, ultimately benefiting their customers with high-quality, reliable components.
The implementation of 4 axis machining technology represents a significant investment for {Company Name}. This technology allows for the simultaneous cutting of multiple surfaces on a workpiece, resulting in faster production cycles and improved accuracy. Additionally, the ability to rotate the workpiece on multiple axes provides greater flexibility in machining complex geometries, ultimately expanding the capabilities of {Company Name} in meeting the diverse needs of their customers.
The addition of 4 axis machining technology to their production capabilities further solidifies {Company Name}'s commitment to providing cutting-edge solutions to their customers. With this new technology, they are better positioned to handle a wider range of projects, from aerospace components to medical device parts, all with the same level of precision and excellence that {Company Name} is known for.
{Company Name} has a long history of innovation and continuous improvement, and the introduction of 4 axis machining technology is just the latest example of their dedication to staying at the forefront of their industry. By constantly investing in the latest advancements in manufacturing technology, {Company Name} remains poised to meet the evolving needs of their customers and adapt to the ever-changing landscape of the manufacturing industry.
The implementation of 4 axis machining technology also represents {Company Name}'s ongoing commitment to efficiency and sustainability. By optimizing their production processes and reducing material waste, they are not only able to increase their output capacity but also reduce their environmental impact—a win-win for both {Company Name} and their customers.
"We are thrilled to introduce 4 axis machining technology to our production capabilities," said the CEO of {Company Name}. "This investment demonstrates our commitment to providing the highest quality components to our customers, while also allowing us to take on more complex projects and deliver them in a timely manner. We are confident that this technology will further enhance our reputation as a leading manufacturing company."
{Company Name} has always been focused on providing exceptional value to their customers through a combination of cutting-edge technology, skilled craftsmanship, and a relentless commitment to excellence. The addition of 4 axis machining technology is yet another step in this ongoing journey, positioning {Company Name} as a top choice for precision engineering solutions.
As {Company Name} continues to usher in the new era of manufacturing with their advanced 4 axis machining technology, they remain dedicated to pushing the boundaries of what is possible, solidifying their position as an industry leader and shaping the future of precision engineering.
Company News & Blog
High-Quality Round Rubber Gaskets Seals for Various Applications
[Company Introduction]With a history dating back to 1960, we are a leading manufacturer and supplier of high-quality rubber gaskets and seals to a wide range of industries such as automotive, aerospace, pharmaceutical, and industrial manufacturing. Our commitment to excellence and constant innovation has solidified our reputation as a trusted partner in providing sealing solutions that meet the rigorous demands of our customers.Our state-of-the-art manufacturing facility is equipped with the latest technology and machinery to ensure precision and consistency in the production of our rubber gaskets and seals. We take pride in our skilled team of engineers and technicians who work tirelessly to develop and improve our products, always striving to stay ahead of industry standards.In line with our dedication to quality, we adhere to strict quality control measures at every stage of the manufacturing process, from sourcing raw materials to the final inspection of finished products. Our ISO 9001 certification is a testament to our unwavering commitment to delivering products of the highest standard to our customers.[News Content]The demand for high-performance rubber gaskets and seals continues to grow across various industries, and we are proud to announce our latest innovation in this space. Our newly developed Round Rubber Gaskets Seals are set to revolutionize the sealing industry with their exceptional performance and durability.Designed to meet the stringent requirements of diverse applications, our Round Rubber Gaskets Seals boast a range of features that set them apart from conventional sealing solutions. The use of premium quality rubber compounds ensures excellent resistance to temperature, pressure, and chemical exposure, making them suitable for use in the most demanding environments.One of the key highlights of our Round Rubber Gaskets Seals is their superior compression set properties, which enables them to maintain a tight and reliable seal over an extended period. This makes them ideal for sealing applications that require long-term performance and minimal maintenance. Additionally, the round design of these gaskets and seals ensures uniform contact pressure, further enhancing their sealing efficiency.The versatility of our Round Rubber Gaskets Seals is another compelling aspect, as they can be customized to suit specific customer requirements. Whether it's a unique size, shape, or material specification, our team of experts is capable of tailoring these sealing solutions to meet the precise needs of our customers, providing them with a truly bespoke sealing solution.Furthermore, sustainability is a key consideration in our product development, and our Round Rubber Gaskets Seals are manufactured with eco-friendly processes and materials. By prioritizing environmental responsibility, we aim to provide our customers with sealing solutions that not only deliver performance but also contribute to a more sustainable future.In addition to the superior performance of our Round Rubber Gaskets Seals, customers can also benefit from our exceptional customer service and technical support. Our team of experienced professionals is always ready to provide assistance and guidance, ensuring that our customers have a seamless experience from product selection to post-installation support.As we introduce our Round Rubber Gaskets Seals to the market, we are confident that they will set a new benchmark for sealing solutions and reinforce our position as a leader in the industry. With their outstanding performance, versatility, and eco-friendly attributes, our Round Rubber Gaskets Seals are poised to meet the evolving needs of our customers and contribute to the advancement of various industries.
High-quality Electroplating Aluminum CNC Turning Parts
Manufacturing industry is undergoing a rapid transformation with the adoption of advanced technologies and innovative strategies to meet the growing demand for high-quality products. One company that is at the forefront of this revolution is {}, a leading manufacturer of precision machined parts and components.Based in {}, the company has built a solid reputation for delivering top-notch products and services to a wide range of industries, including automotive, aerospace, medical, and electronics. With a strong focus on quality and precision, {} has invested heavily in advanced manufacturing technologies to ensure that their customers receive the best possible solutions for their specific needs.One of the key capabilities that set {} apart from their competitors is their expertise in electroplating aluminum CNC turning parts. This specialized process involves coating aluminum parts with a thin layer of metal to enhance their surface properties and improve their performance in various applications. By leveraging their state-of-the-art CNC turning machines and extensive knowledge of electroplating techniques, {} is able to produce high-precision, high-performance aluminum parts that meet the stringent requirements of their customers.The electroplating process at {} begins with the preparation of the aluminum parts, which are carefully cleaned and pretreated to ensure optimal adhesion of the plating material. The parts are then placed in a specialized electroplating bath, where a thin layer of metal is deposited onto their surface through an electrochemical reaction. This metal coating not only improves the appearance of the parts but also provides enhanced corrosion resistance, wear resistance, and electrical conductivity.With their commitment to excellence, {} has perfected the art of electroplating aluminum CNC turning parts, offering their customers a range of benefits, including improved part longevity, reduced maintenance costs, and enhanced performance in demanding applications. Furthermore, the company's ability to tailor the plating process to meet the unique requirements of each customer's project underscores their dedication to providing customized solutions that exceed expectations.In addition to their expertise in electroplating, {} also offers a comprehensive range of CNC turning services, utilizing the latest computer-controlled machining centers to produce complex, high-precision parts with utmost efficiency. Their team of skilled machinists and engineers works closely with customers to understand their specific needs, providing valuable insights and technical expertise to optimize the design and manufacturing processes.The combination of advanced machining capabilities, in-depth material knowledge, and a commitment to quality makes {} a preferred partner for customers seeking reliable and cost-effective solutions for their precision machined part needs. Whether it's creating intricate components for aerospace applications or producing durable parts for the automotive industry, {} has the expertise and resources to deliver exceptional results.Looking ahead, {} is set to further expand their electroplating and CNC turning capabilities, leveraging emerging technologies and industry best practices to stay ahead of the curve. By continuing to invest in the latest equipment and talent, the company aims to strengthen its position as a leading provider of high-quality precision machined parts, meeting the evolving needs of its customers across industries.In conclusion, the electroplating aluminum CNC turning parts expertise of {} is a testament to their unwavering commitment to quality, innovation, and customer satisfaction. With a solid track record of delivering excellence, the company is poised to lead the way in the ever-evolving manufacturing landscape, setting new benchmarks for precision and performance in the industry.
Custom CNC Drilling Services for Precision Machining
CNC Drilling Services: Revolutionizing the Manufacturing IndustryIn today's fast-paced and competitive manufacturing industry, precision and efficiency are paramount. Manufacturers are constantly seeking new and innovative ways to improve their processes and deliver high-quality products to their customers. One technology that has revolutionized the manufacturing industry is CNC drilling services.CNC drilling, or computer numerical control drilling, is a modern machining process that utilizes automated machinery to produce precise and accurate holes in materials such as metal, plastic, and wood. This technology has significantly improved the efficiency and reliability of drilling processes, making it an essential tool for manufacturers across various industries.One company at the forefront of CNC drilling services is {}, a leading provider of precision machining and manufacturing solutions. With state-of-the-art equipment and a team of highly skilled engineers and technicians, {} has established itself as a trusted partner for businesses seeking high-quality drilling services.{}'s CNC drilling services offer a wide range of capabilities, including drilling, tapping, and countersinking, with the ability to produce complex hole patterns and geometries with exceptional accuracy. The company's advanced CNC machinery allows for rapid production turnaround times, making it an ideal solution for both prototyping and high-volume production runs.One of the key advantages of {}'s CNC drilling services is their ability to consistently deliver tight tolerances and high-quality finishes, ensuring that components and parts meet the most demanding specifications. This level of precision is essential for industries such as aerospace, automotive, medical, and electronics, where even the smallest deviation can have significant consequences.In addition to precision drilling, {} offers a range of value-added services to support their customers' diverse manufacturing needs. These services include design assistance, material selection guidance, and finishing processes such as anodizing, plating, and painting. By providing a comprehensive suite of services, {} can serve as a one-stop shop for manufacturers looking to streamline their production processes.With a commitment to continuous improvement and investment in the latest technology, {} has positioned itself as a leader in the CNC drilling services industry. The company's dedication to quality, reliability, and customer satisfaction has earned them a strong reputation in the market, attracting a diverse customer base across various sectors.Beyond delivering high-quality products, {} is also focused on sustainability and environmental responsibility. The company actively seeks ways to minimize waste, reduce energy consumption, and utilize eco-friendly materials and processes wherever possible. By aligning their operations with sustainable practices, {} aims to not only meet the needs of their customers but also contribute to a greener and more responsible manufacturing industry.As the manufacturing industry continues to evolve, the demand for precision machining and drilling services will only grow. With its advanced capabilities, commitment to excellence, and customer-focused approach, {} is well-positioned to meet the evolving needs of manufacturers and drive innovation in the CNC drilling services space.In conclusion, CNC drilling services have become a cornerstone of modern manufacturing, enabling businesses to produce high-quality components with unparalleled precision and efficiency. Companies like {} are leading the way in delivering cutting-edge drilling solutions, and their dedication to quality, innovation, and sustainability will undoubtedly shape the future of the manufacturing industry.
Ultimate Guide to Two Shot Moulding: Benefits and Techniques Explained
Innovative Two Shot Moulding Process Revolutionizes Manufacturing at {}{} is a leading manufacturer that specializes in providing innovative solutions for the automotive, medical, consumer goods, and electronics industries. With a commitment to delivering high-quality products and exceptional service, the company has established itself as a trusted partner for customers around the globe. Recently, {} has introduced a groundbreaking two shot moulding process that is revolutionizing the manufacturing industry and setting new standards for efficiency and precision.Two shot moulding, also known as dual-shot moulding or double injection moulding, is a manufacturing process that allows for the production of complex, multi-material components in a single operation. This process involves injecting two different materials into a single mould, resulting in a finished product that combines the properties of both materials. {}'s two shot moulding process has been hailed as a game-changer in the industry, allowing for the creation of components that were previously thought to be too complex or costly to produce.The key to {}'s two shot moulding process lies in the company's state-of-the-art manufacturing facilities and cutting-edge technology. With a team of skilled engineers and technicians, {} has developed a proprietary two shot moulding process that delivers unmatched precision and repeatability. This advanced process allows for the efficient production of high-quality, multi-material components with a level of complexity and intricacy that was previously unattainable.One of the major advantages of {}'s two shot moulding process is its ability to streamline the production of complex components. By eliminating the need for multiple manufacturing operations and assembly processes, this innovative process reduces lead times and production costs while improving overall product quality. In addition, {}'s two shot moulding process enables the creation of components with integrated functionality and improved aesthetics, opening up new design possibilities for product developers.The automotive industry has been one of the primary beneficiaries of {}'s two shot moulding process. With the demand for lightweight, durable, and aesthetically pleasing components on the rise, automotive manufacturers have turned to {} for innovative solutions. The company's two shot moulding process has been instrumental in the production of multi-material components for interior and exterior applications, such as decorative trims, buttons, and knobs, as well as functional components like dashboard panels and handles.In the medical field, {}'s two shot moulding process has opened up new possibilities for the production of advanced medical devices and equipment. By combining different materials with varying properties, such as rigid and flexible plastics, the company has been able to create components with enhanced functionality and ergonomics. This has led to the development of innovative medical products that are not only more effective and efficient but also more comfortable for patients and healthcare professionals.Consumer goods and electronics manufacturers have also turned to {} for their two shot moulding needs. Whether it's the production of complex housings for electronic devices, multi-material grips for handheld tools, or stylish and durable consumer products, {}'s two shot moulding process has proven to be a game-changer. By leveraging this advanced manufacturing technology, the company has helped its clients bring new, innovative products to market, setting them apart from the competition.As {} continues to push the boundaries of manufacturing innovation with its two shot moulding process, the company remains committed to delivering exceptional value to its customers. By investing in research and development, and embracing the latest advancements in manufacturing technology, {} is poised to lead the industry into a new era of manufacturing excellence. With its unwavering dedication to quality, innovation, and customer satisfaction, {} is truly redefining the possibilities of modern manufacturing.
High-Quality Aluminum Die Casting Services for Various Industries
Aluminum Die Casting: A Game-Changer in the Manufacturing IndustryIn today's highly competitive manufacturing industry, companies are constantly seeking ways to improve efficiency, reduce costs, and enhance the overall quality of their products. One of the key technologies that has been making a significant impact in this regard is aluminum die casting. Featured as an integral part of the company’s manufacturing process, aluminum die casting has revolutionized the way products are made. With its ability to produce complex and intricately shaped parts with high precision, aluminum die casting has become the go-to method for many industries, including automotive, aerospace, and electronics.At the forefront of this industry-leading technology is {Company Name}, a renowned company with a sterling reputation for excellence in the field of aluminum die casting. With state-of-the-art facilities and a team of highly skilled professionals, {Company Name} has been leading the way in delivering high-quality aluminum die casting solutions to its clients.Aluminum die casting is a process that involves injecting molten aluminum into a steel mold, known as a die, at high pressures. This results in the production of parts that are extremely durable, with excellent mechanical properties and low porosity. The versatility of this process allows for the production of a wide range of complex shapes and sizes, making it an ideal choice for a variety of applications.One of the key advantages of aluminum die casting is its cost-effectiveness. The high-speed production capabilities and the ability to produce net-shaped parts with minimal secondary operations make it a highly efficient manufacturing process. This, in turn, leads to significant cost savings for companies, ultimately translating to a competitive edge in the market.Furthermore, the lightweight nature of aluminum makes it an ideal material for applications in industries such as automotive and aerospace, where weight reduction is a critical factor. Aluminum die cast parts offer high strength-to-weight ratios, making them an excellent choice for demanding applications that require both strength and durability.{Company Name} has been at the forefront of innovation in aluminum die casting, constantly pushing the boundaries of what is possible in terms of part complexity, precision, and quality. Their extensive experience in the industry, combined with their commitment to continuous improvement, has enabled them to consistently deliver exceptional results to their clients.The company's dedication to quality is reflected in their stringent quality control measures and adherence to industry standards. By utilizing advanced simulation and testing techniques, {Company Name} ensures that each part produced through aluminum die casting meets the highest standards of quality and performance.In addition to aluminum die casting, {Company Name} also offers a range of value-added services, including machining, finishing, and assembly. This comprehensive approach allows them to provide end-to-end solutions to their clients, further cementing their position as a trusted partner in the manufacturing industry.With the ever-increasing demand for high-quality, precision-engineered parts, the future of aluminum die casting looks brighter than ever. {Company Name} remains committed to staying at the forefront of this industry, continuously investing in the latest technologies and processes to meet the evolving needs of their clients.In conclusion, aluminum die casting has undoubtedly emerged as a game-changer in the manufacturing industry, and {Company Name} is leading the charge with its unparalleled expertise and dedication to excellence. As the industry continues to evolve, {Company Name} remains poised to deliver innovative solutions that will shape the future of manufacturing for years to come.
Understanding the Process and Benefits of Plastic Insert Molding
Plastic Insert Molding Offers Enhanced Precision and Efficiency for Company {}In today's fast-paced manufacturing environment, precision and efficiency are key factors in ensuring the success of a company's production process. One method that has gained significant attention in recent years for achieving these goals is plastic insert molding. This advanced manufacturing technique has revolutionized the way companies produce plastic parts by combining precision and efficiency into one seamless process. One company that has adopted this innovative approach to manufacturing is {}.{} is a leading manufacturer in the plastic injection molding industry, specializing in providing high-quality plastic components for a wide range of industries, including automotive, healthcare, consumer goods, and electronics. With a commitment to excellence and a focus on innovation, {} is constantly exploring new technologies and processes to improve the quality and efficiency of its production methods.One of the technologies that has significantly impacted {}'s manufacturing capabilities is plastic insert molding. This process involves molding thermoplastic material around metal or plastic inserts, resulting in a more precise and durable product. By incorporating plastic insert molding into their production process, {} has been able to create complex, multi-material components with a high level of precision and efficiency.One of the key benefits of plastic insert molding is its ability to reduce the need for secondary assembly processes, such as welding or adhesives. This not only saves time and labor costs but also results in a more reliable and consistent end product. {} has capitalized on this advantage by offering its customers a streamlined manufacturing process that delivers high-quality plastic components with shorter lead times and reduced overall production costs.In addition to its efficiency, plastic insert molding also provides improved part consistency and reliability. The process allows for tighter tolerances and better control over material distribution, resulting in parts that are more resistant to wear and tear. This is particularly beneficial for industries such as automotive and healthcare, where the performance and durability of plastic components are critical.Another crucial advantage of plastic insert molding is its ability to create complex geometries and features in a single process. This makes it possible for {} to produce intricate and detailed plastic parts that would be difficult or impossible to achieve with traditional manufacturing methods. As a result, the company is able to offer its customers innovative solutions that meet the evolving demands of their respective industries.{}'s investment in plastic insert molding technology has positioned the company as a leader in the manufacturing of precision plastic components. By leveraging the advantages of this advanced manufacturing process, {} has been able to enhance its production capabilities and expand its product offerings to meet the diverse needs of its customers.With a strong emphasis on quality, innovation, and customer satisfaction, {} is committed to continuing its investment in advanced manufacturing technologies. As the company looks to the future, it remains dedicated to pushing the boundaries of what is possible in plastic component manufacturing, delivering cutting-edge solutions that drive success for its customers.In conclusion, plastic insert molding has revolutionized the way {} produces plastic components, offering enhanced precision, efficiency, and reliability. By embracing this advanced manufacturing technique, {} has solidified its position as a leader in the industry, delivering high-quality plastic parts that meet the diverse needs of its customers. As the company continues to invest in innovative technologies, it is poised to uphold its commitment to excellence and drive success for its customers in the ever-evolving manufacturing landscape.
Advanced 4 Axis Machining: What You Need to Know
{Company Name} Introduces Advanced 4 Axis Machining TechnologyIn the ever-evolving world of manufacturing and precision engineering, staying ahead of the curve is crucial for any company looking to maintain a competitive edge. That's why {Company Name}, a leader in the manufacturing industry, has recently announced the introduction of advanced 4 axis machining technology to their production line.This new technology allows {Company Name} to offer an even greater level of precision and efficiency in their machining processes, ultimately benefiting their customers with high-quality, reliable components.The implementation of 4 axis machining technology represents a significant investment for {Company Name}. This technology allows for the simultaneous cutting of multiple surfaces on a workpiece, resulting in faster production cycles and improved accuracy. Additionally, the ability to rotate the workpiece on multiple axes provides greater flexibility in machining complex geometries, ultimately expanding the capabilities of {Company Name} in meeting the diverse needs of their customers.The addition of 4 axis machining technology to their production capabilities further solidifies {Company Name}'s commitment to providing cutting-edge solutions to their customers. With this new technology, they are better positioned to handle a wider range of projects, from aerospace components to medical device parts, all with the same level of precision and excellence that {Company Name} is known for.{Company Name} has a long history of innovation and continuous improvement, and the introduction of 4 axis machining technology is just the latest example of their dedication to staying at the forefront of their industry. By constantly investing in the latest advancements in manufacturing technology, {Company Name} remains poised to meet the evolving needs of their customers and adapt to the ever-changing landscape of the manufacturing industry.The implementation of 4 axis machining technology also represents {Company Name}'s ongoing commitment to efficiency and sustainability. By optimizing their production processes and reducing material waste, they are not only able to increase their output capacity but also reduce their environmental impact—a win-win for both {Company Name} and their customers."We are thrilled to introduce 4 axis machining technology to our production capabilities," said the CEO of {Company Name}. "This investment demonstrates our commitment to providing the highest quality components to our customers, while also allowing us to take on more complex projects and deliver them in a timely manner. We are confident that this technology will further enhance our reputation as a leading manufacturing company."{Company Name} has always been focused on providing exceptional value to their customers through a combination of cutting-edge technology, skilled craftsmanship, and a relentless commitment to excellence. The addition of 4 axis machining technology is yet another step in this ongoing journey, positioning {Company Name} as a top choice for precision engineering solutions.As {Company Name} continues to usher in the new era of manufacturing with their advanced 4 axis machining technology, they remain dedicated to pushing the boundaries of what is possible, solidifying their position as an industry leader and shaping the future of precision engineering.
Aluminum CNC Turning Parts for Electroplating - A Complete Guide
Metal manufacturing company, based in [location], has recently announced the launch of their new product, Electroplating Aluminum CNC turning parts. This innovative product has been developed to meet the growing demand for high-quality aluminum parts in various industries such as automotive, aerospace, and electronics.The Electroplating Aluminum CNC turning parts are designed to be versatile and durable, making them suitable for a wide range of applications. With their high precision and tight tolerances, these parts are capable of meeting the strict requirements of modern manufacturing processes. The company has invested in state-of-the-art CNC turning machines to ensure the highest quality and consistency in the production of these parts.In addition to their exceptional quality, the Electroplating Aluminum CNC turning parts also offer excellent corrosion resistance and a sleek, attractive finish. This makes them ideal for use in outdoor, marine, and other harsh environments where protection against corrosion is essential. The electroplating process in which the parts undergo enhances their surface hardness and wear resistance, making them suitable for long-term use.The company's decision to develop and manufacture Electroplating Aluminum CNC turning parts comes as a response to the increasing demand for such products in both domestic and international markets. With the rising trend towards lightweight and high-performance materials in various industries, the company saw an opportunity to expand its product offering and cater to the evolving needs of its customers.Furthermore, the company's extensive experience and expertise in metal manufacturing have allowed them to develop and produce Electroplating Aluminum CNC turning parts that meet the highest industry standards. Their dedicated team of engineers and technicians has worked tirelessly to ensure that these parts deliver exceptional performance and reliability in the most demanding applications.The development and launch of these Electroplating Aluminum CNC turning parts are a testament to the company's commitment to innovation and customer satisfaction. They have continuously invested in research and development to bring cutting-edge products to the market, and the new parts are a reflection of their dedication to staying at the forefront of the industry."We are thrilled to introduce our new Electroplating Aluminum CNC turning parts to the market," said the company's spokesperson. "We believe that these parts will set a new standard for quality and performance in the industry, and we are confident that they will meet the diverse needs of our customers. With our advanced manufacturing capabilities and stringent quality control processes, we are well-positioned to deliver these parts to customers around the world."The Electroplating Aluminum CNC turning parts are now available for purchase, and the company is ready to fulfill orders from customers across different industries. With their strong commitment to customer satisfaction and their ability to tailor solutions to specific requirements, the company is confident that these parts will be well-received in the market.As the demand for high-quality aluminum parts continues to grow, the launch of the Electroplating Aluminum CNC turning parts represents a significant milestone for the company and reinforces its position as a leading provider of metal manufacturing solutions. With their dedication to innovation and excellence, the company is poised to make a lasting impact in the industry and meet the evolving needs of its customers.
High-quality CNC turning parts manufacturers in China: a comprehensive guide
China CNC Turning Parts Manufacturers, a leading manufacturer of precision CNC turning parts, has recently announced the expansion of its production capacity to meet the increasing demand for high-quality CNC turning parts in the global market. The company, which specializes in the production of custom CNC turning parts for a wide range of industries including automotive, aerospace, electronics, and more, has invested heavily in state-of-the-art equipment and technology to ensure that it can continue to provide its customers with the highest quality products.With a strong focus on quality and precision, China CNC Turning Parts Manufacturers has quickly established itself as a trusted partner for businesses looking for reliable and cost-effective CNC turning parts. The company's commitment to quality is reflected in its rigorous quality control processes, which ensure that every part that leaves its facility meets the highest industry standards. In addition, the company's team of skilled engineers and technicians work closely with customers to understand their unique needs and provide customized solutions that meet or exceed their expectations.The expansion of China CNC Turning Parts Manufacturers' production capacity comes at a time when the demand for precision CNC turning parts is at an all-time high. As industries continue to advance and evolve, the need for high-quality, custom-made parts has become increasingly important. By investing in the latest technology and equipment, China CNC Turning Parts Manufacturers is positioning itself to meet this demand and continue to be a leader in the industry."We are excited to announce the expansion of our production capacity," said a spokesperson for China CNC Turning Parts Manufacturers. "This investment represents our commitment to meeting the growing demand for precision CNC turning parts. We are confident that our expanded capabilities will enable us to better serve our customers and provide them with the highest quality products."In addition to expanding its production capacity, China CNC Turning Parts Manufacturers is also focusing on streamlining its manufacturing processes to improve efficiency and reduce lead times. By implementing lean manufacturing principles and investing in automation technology, the company aims to offer faster turnaround times without compromising on quality. This will allow customers to receive their custom CNC turning parts in a timely manner, helping to keep their own production processes on schedule.As China CNC Turning Parts Manufacturers continues to grow and expand, the company remains committed to its core values of quality, innovation, and customer satisfaction. With a strong focus on research and development, the company is constantly exploring new technologies and techniques to improve its products and services. This dedication to continuous improvement has earned China CNC Turning Parts Manufacturers a reputation as a reliable and forward-thinking partner for businesses in need of precision CNC turning parts."We are always looking for ways to improve and innovate," added the spokesperson. "Our goal is to provide our customers with the best possible products and services, and we will continue to invest in our people, processes, and technology to achieve that goal."As China CNC Turning Parts Manufacturers continues to expand its production capacity and improve its manufacturing processes, the company is well-positioned to meet the increasing demand for custom CNC turning parts in the global market. With a strong focus on quality, innovation, and customer satisfaction, the company is poised to remain a leader in the industry for years to come.
Understanding the Significance of Prototype Injection in Manufacturing Processes
Prototype Injection, a leading injection molding company, has recently announced the development of a new and innovative injection molding technology that is set to revolutionize the industry. This technology, which has been in development for the past two years, promises to significantly reduce production times and costs, while also improving the quality and precision of the final products.At the core of this new technology is a proprietary molding process that allows for the creation of complex and intricate molds with unprecedented speed and accuracy. This process, which has been patented by Prototype Injection, utilizes state-of-the-art computer-aided design and manufacturing (CAD/CAM) software to create highly detailed and precise molds that were previously thought to be impossible to produce.In addition to the new molding process, Prototype Injection has also developed a range of proprietary materials that are specifically designed to work with this technology. These materials, which have been extensively tested and proven to be highly durable and reliable, are set to further enhance the capabilities of the new injection molding process."We are extremely excited to introduce this new technology to the market," said John Smith, CEO of Prototype Injection. "We believe that it has the potential to completely transform the injection molding industry and open up new possibilities for manufacturers in a wide range of industries."In addition to the development of this new technology, Prototype Injection also prides itself on its commitment to sustainability and environmental responsibility. The company has implemented a number of initiatives to reduce its environmental impact, including the use of recycled materials and the implementation of energy-efficient manufacturing processes."We believe that it is our responsibility as a leading manufacturer to minimize our impact on the environment," said Smith. "That is why we have made sustainability a top priority in our business operations."Prototype Injection has also invested heavily in the training and development of its workforce, ensuring that its employees are highly skilled and knowledgeable in the latest manufacturing techniques and technologies. This commitment to excellence has helped the company to maintain its position as a leader in the injection molding industry."We believe that our employees are our most valuable asset," said Smith. "That is why we are dedicated to providing them with the training and support they need to excel in their roles and contribute to the success of our company."With the introduction of this new injection molding technology, Prototype Injection is poised to solidify its position as a leader in the industry. The company's commitment to innovation, sustainability, and employee development sets it apart from its competitors and positions it for continued success in the years to come."We are confident that this new technology will revolutionize the injection molding industry," said Smith. "We are excited to see the positive impact it will have on our business, as well as on the manufacturing industry as a whole.