Benefits of Laser Prototyping for Rapid Product Development
By:Admin
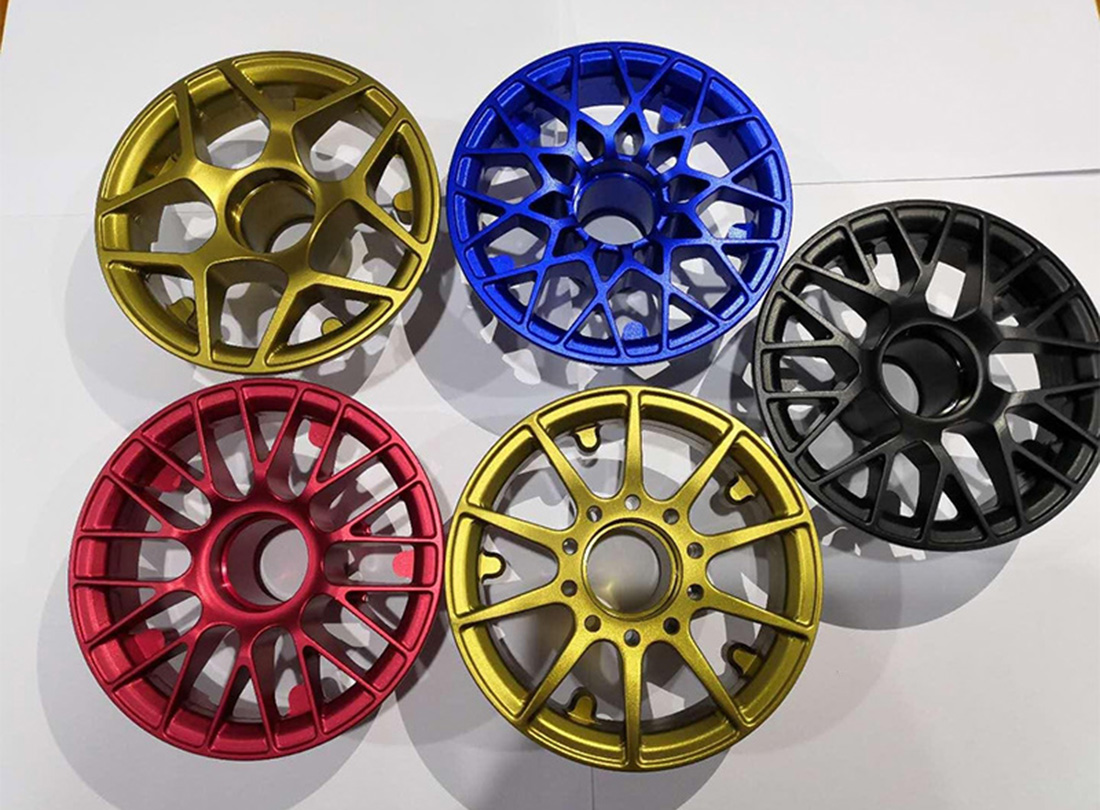
The manufacturing industry is constantly evolving, with new technologies and advancements changing the way products are developed and produced. One of the most recent and groundbreaking innovations in the industry is the use of laser prototyping technology. This cutting-edge technology is revolutionizing the manufacturing process by allowing companies to create high-quality prototypes and production parts with unmatched speed and precision.
Laser prototyping, also known as rapid prototyping, is a process that uses a high-powered laser to selectively sinter powdered materials, such as metals, plastics, or ceramics, layer by layer to create three-dimensional objects. This technology is incredibly versatile and can be used to produce complex geometries and intricate designs that would be difficult or impossible to achieve using traditional manufacturing methods. Furthermore, laser prototyping allows for rapid iteration and customization, making it an ideal solution for companies in need of quick turnaround times and flexible production capabilities.
One company at the forefront of laser prototyping technology is {}. Founded in 1999, {} has been a pioneer in the development and implementation of advanced laser systems for a wide range of industrial applications. With a strong focus on innovation and customer satisfaction, {} has continuously pushed the boundaries of what is possible with laser technology, creating solutions that have redefined the manufacturing industry.
{}'s laser prototyping systems utilize state-of-the-art laser sources and advanced powder bed fusion techniques to deliver exceptional part quality and dimensional accuracy. The company's integrated software and hardware solutions enable precise control over the laser sintering process, allowing for the creation of highly detailed and functional prototypes and production parts. In addition, {}'s laser systems are designed for scalability, making them suitable for small-scale rapid prototyping as well as large-scale industrial production.
The benefits of laser prototyping technology extend beyond its technical capabilities. By streamlining the product development cycle and reducing the need for expensive tooling and machining, laser prototyping can significantly lower production costs and time to market. This has a direct impact on a company's bottom line and overall competitiveness in the market. Furthermore, the ability to quickly iterate and test designs allows for more efficient development processes and ultimately leads to better end products.
In recent years, {} has seen a surge in demand for its laser prototyping systems from a diverse range of industries, including aerospace, automotive, medical, and consumer goods. This reflects the growing recognition of the value that laser prototyping brings to the table in terms of innovation, efficiency, and quality. As the manufacturing industry continues to evolve, it is clear that laser prototyping will play a crucial role in shaping the future of product development and production.
With a strong track record of delivering cutting-edge laser solutions and a commitment to empowering its customers with the latest technology, {} is well-positioned to lead the charge in the widespread adoption of laser prototyping. The company's dedication to pushing the boundaries of what is possible with laser technology, coupled with its focus on customer satisfaction, has positioned it as a trusted partner for companies looking to harness the power of laser prototyping to gain a competitive edge in their respective industries.
In conclusion, laser prototyping technology is a game-changer for the manufacturing industry, offering unparalleled speed, precision, and flexibility in the production of prototypes and production parts. With {} leading the charge in the development and implementation of advanced laser prototyping systems, the future of manufacturing looks brighter than ever. As companies continue to embrace this revolutionary technology, the possibilities for innovation and success are endless.
Company News & Blog
The Ultimate Guide to Laser-Cut Foam Board: Tips, Techniques, and Benefits
Laser Cut Foam Board: Revolutionizing the IndustryIn the ever-evolving world of design and manufacturing, staying ahead of the curve is essential for companies seeking to remain competitive. This is especially true for the [Company Name], a leading provider of high-quality foam board solutions. The company has recently announced the launch of a new product that is set to revolutionize the industry – Laser Cut Foam Board.Laser Cut Foam Board is a cutting-edge material that combines the versatility of foam board with the precision of laser cutting technology. This innovative product offers a wide range of benefits, making it ideal for a variety of applications in industries such as packaging, signage, and model making.One of the key advantages of Laser Cut Foam Board is its high level of precision. The use of laser cutting technology ensures that each piece is cut to exact specifications, resulting in a perfect fit every time. This level of precision is especially important in industries where accuracy is paramount, such as in the creation of intricate packaging designs or detailed signage.Another benefit of Laser Cut Foam Board is its versatility. The material is available in a variety of thicknesses and colors, making it suitable for a wide range of applications. Whether it's creating eye-catching displays or building detailed architectural models, Laser Cut Foam Board offers the flexibility needed to bring any design to life.In addition to its precision and versatility, Laser Cut Foam Board also offers superior durability. The material is resistant to moisture, chemicals, and aging, ensuring that it can withstand the rigors of daily use without deteriorating. This durability makes it an ideal choice for long-lasting applications, such as outdoor signage or protective packaging.The introduction of Laser Cut Foam Board reflects [Company Name]'s commitment to innovation and meeting the changing needs of its customers. The company has a long history of providing high-quality foam board solutions, and the launch of this new product further solidifies its position as a leader in the industry.With a state-of-the-art manufacturing facility and a team of skilled professionals, [Company Name] is well-equipped to produce Laser Cut Foam Board to the highest standards. The company's dedication to quality and customer satisfaction ensures that each piece of Laser Cut Foam Board meets the strictest industry standards, providing customers with confidence in the reliability and performance of the product.In addition to its commitment to quality, [Company Name] is also dedicated to environmental sustainability. Laser Cut Foam Board is a recyclable material, underscoring the company's commitment to reducing its impact on the environment. By offering a product that is both high-performing and environmentally friendly, [Company Name] is taking a proactive approach to corporate responsibility.As [Company Name] continues to drive innovation in the foam board industry, the launch of Laser Cut Foam Board represents a significant milestone in the company's history. With its unparalleled precision, versatility, and durability, this new product is poised to revolutionize the way designers and manufacturers approach their projects. The introduction of Laser Cut Foam Board underscores [Company Name]'s position as a leader in the industry and sets a new standard for foam board solutions.With its cutting-edge technology and unwavering commitment to quality, [Company Name] is paving the way for a new era of design and manufacturing. As the company continues to push the boundaries of what is possible, one thing is certain – the future is bright for both [Company Name] and the industries it serves.
Creating High-Quality Injection Molds: A Guide for Manufacturers
Injection Mold Making: Innovative Solutions for High-Quality ManufacturingInjection mold making is an essential process in the manufacturing industry, and it plays a critical role in the production of various products. From automotive parts to consumer goods, injection molds are used to create the intricate and precise components that make up these products. In this regard, [Company Name] has been a leading player in the injection mold making industry, offering innovative solutions for high-quality manufacturing.[Company Name] is a well-established company with a strong reputation for its expertise in injection mold making. With a focus on delivering precision, reliability, and efficiency, the company has been catering to the diverse needs of the manufacturing sector. [Company Name] utilizes the latest technologies and industry best practices to ensure that its injection molds meet the highest standards of quality and performance.One of the key strengths of [Company Name] lies in its ability to customize injection molds according to the specific requirements of its clients. The company understands that every product is unique, and therefore, it offers tailored solutions to meet the exact needs of its customers. Whether it is the design, material selection, or production process, [Company Name] works closely with its clients to deliver injection molds that are perfectly aligned with their manufacturing goals.In addition to customization, [Company Name] also emphasizes innovation in its injection mold making process. The company continuously invests in research and development to explore new materials, technologies, and techniques that can enhance the quality and efficiency of its molds. This commitment to innovation has allowed [Company Name] to stay ahead of the curve and offer cutting-edge solutions to its clients.Furthermore, [Company Name] takes pride in its state-of-the-art manufacturing facilities, which are equipped with advanced machinery and quality control systems. The company follows strict quality assurance measures at every stage of the production process to ensure that its injection molds meet the highest standards. From concept to delivery, [Company Name] maintains a rigorous approach to quality, which has earned the trust of its clients over the years.Another notable aspect of [Company Name]’s injection mold making is its commitment to sustainability. The company is conscious of its environmental impact and strives to minimize its carbon footprint through eco-friendly manufacturing practices. By utilizing recyclable materials and energy-efficient processes, [Company Name] ensures that its injection molds not only meet performance requirements but also adhere to sustainable principles.Moreover, [Company Name]’s dedication to customer satisfaction sets it apart in the injection mold making industry. The company places great importance on building strong and lasting relationships with its clients, understanding their needs, and exceeding their expectations. By offering responsive support, timely delivery, and competitive pricing, [Company Name] has become a trusted partner for numerous manufacturing companies.In conclusion, injection mold making is a critical aspect of the manufacturing process, and [Company Name] has established itself as a reliable and innovative provider in this field. With a focus on customization, innovation, quality, sustainability, and customer satisfaction, the company continues to deliver high-performance injection molds for a wide range of applications. As manufacturing industries seek to enhance their production capabilities, [Company Name] remains a go-to solution for their injection mold making needs.
Durable Rubber Gasket for Industrial Use: A Comprehensive Guide
Square Rubber Gasket, a leading manufacturer in the rubber gasket industry, has recently unveiled its latest product designed to meet the ever-growing demand for high-quality and reliable gaskets in various industrial applications. With a history of excellence and innovation, Square Rubber Gasket has set itself apart as a trusted source for superior rubber gaskets.Established in [year], Square Rubber Gasket has built a solid reputation for delivering top-notch gaskets that excel in performance, durability, and effectiveness. The company is committed to utilizing advanced manufacturing techniques and high-quality materials to produce gaskets that meet or exceed industry standards. With a focus on customer satisfaction and engineering excellence, Square Rubber Gasket has become a preferred choice for businesses seeking reliable sealing solutions.The newly launched square rubber gasket is the latest addition to Square Rubber Gasket's extensive product line. Engineered to precise specifications, this gasket is designed to provide exceptional sealing performance in a wide range of applications. The square shape of the gasket offers unique advantages, including enhanced stability and a tight seal, making it an ideal choice for various industrial equipment and machinery."We are thrilled to introduce our latest square rubber gasket to the market," said [spokesperson]. "This new product showcases our dedication to innovation and our commitment to meeting the evolving needs of our customers. We are confident that this gasket will deliver outstanding performance and reliability, further solidifying our position as a leader in the industry."The square rubber gasket is manufactured using advanced rubber compounds that offer superior resilience, resistance to heat and chemicals, and long-lasting durability. These properties make the gasket suitable for use in demanding environments where reliable sealing is crucial. Additionally, the square shape of the gasket provides enhanced stability and uniform compression, ensuring a tight and secure seal.One of the key advantages of the square rubber gasket is its versatility. It can be used across various industries, such as automotive, aerospace, marine, manufacturing, and many others. Whether it is sealing components in heavy machinery or providing insulation in electrical enclosures, the square rubber gasket offers a reliable solution for a wide range of applications.Square Rubber Gasket's commitment to quality and excellence extends beyond its products. The company's dedication to providing exceptional customer service and technical support has earned it a loyal and satisfied customer base. With a team of experienced engineers and industry experts, Square Rubber Gasket works closely with its clients to understand their specific sealing requirements and provide customized solutions that meet their needs.As a responsible and environmentally conscious manufacturer, Square Rubber Gasket takes great care to ensure its production processes are sustainable and eco-friendly. The company complies with all relevant regulations and standards, and it continuously seeks to minimize its environmental impact through efficient use of resources and waste reduction.In conclusion, Square Rubber Gasket's latest square rubber gasket represents a significant advancement in sealing technology. With its precision engineering, exceptional performance, and versatility, this gasket is poised to set new standards in the industry. As Square Rubber Gasket continues to push the boundaries of innovation and quality, it remains a trusted partner for businesses seeking reliable sealing solutions. With its unwavering commitment to excellence and customer satisfaction, Square Rubber Gasket is set to maintain its position as a leader in the rubber gasket industry.
High-Quality CNC Turned Components for Your Manufacturing Needs
CNC turned components are a crucial part of modern manufacturing processes. These components are used in a wide range of industries, including automotive, aerospace, electronics, and medical device manufacturing. The precision and high quality of CNC turned components make them popular in the production of complex and intricate parts.With the advancement of technology, the demand for high-quality CNC turned components has been increasing. As a result, many manufacturers are now turning to CNC machining to produce these components. One such company that has been leading the way in the manufacturing of CNC turned components is {}.{} is a leading manufacturer of CNC turned components, specializing in producing high precision parts for a variety of industries. With state-of-the-art facilities and a team of skilled engineers and technicians, {} has positioned itself as a industry leader in the production of CNC turned components.The company has a wide range of CNC machining capabilities, including turning, milling, drilling, and grinding. This allows them to produce components with tight tolerances and complex geometries, meeting the high standards required by their customers.In addition to their advanced machining capabilities, {} also focuses on quality control and inspection processes to ensure that every component they produce meets the highest standards. This commitment to quality has earned {} a reputation for delivering precision components that meet and exceed the expectations of their customers.One of the key advantages of CNC turned components is their ability to be produced in large quantities with consistent quality. This makes them an ideal choice for manufacturers who require high volume production of intricate parts. {} has the capacity to handle large production runs, making them a preferred supplier for many companies in need of CNC turned components.As the demand for precision components continues to grow, {} is continuously investing in the latest CNC machining technology to stay ahead of the competition. By staying at the forefront of innovation, {} is able to offer their customers the highest quality CNC turned components with shorter lead times and competitive pricing.In addition to their commitment to quality and innovation, {} prides itself on providing exceptional customer service. Their team of experts works closely with their clients to understand their specific needs and provide tailored solutions to meet those requirements. This personalized approach has helped {} build strong, long-term relationships with their customers, making them a trusted partner in the manufacturing industry.With their dedication to quality, innovation, and customer satisfaction, {} continues to be a leading force in the production of CNC turned components. As the demand for precision parts continues to rise, {} is well-equipped to meet the needs of the industry and deliver top-notch components to their customers.In conclusion, CNC turned components play a critical role in modern manufacturing processes, and {} has established itself as a leader in producing high-quality, precision components for a wide range of industries. With their advanced machining capabilities, commitment to quality, and exceptional customer service, {} is well-positioned to meet and exceed the demands of the evolving manufacturing landscape.
Innovative CNC Foam Prototype for Precision Engineering
CNC Foam Prototype Technology Revolutionizing Manufacturing ProcessIn recent years, CNC foam prototyping technology has revolutionized the manufacturing process, allowing for the creation of intricate and precise foam prototypes with incredible speed and accuracy. This cutting-edge technology has been embraced by a wide range of industries, from automotive and aerospace to medical and consumer electronics, and has fundamentally changed the way products are developed and brought to market.One company at the forefront of this technology is {}. With their state-of-the-art CNC foam prototyping facility, they have been able to produce foam prototypes that are not only highly detailed and accurate, but also incredibly efficient to manufacture. This has greatly reduced the time and cost associated with the prototyping process, allowing their clients to bring new products to market faster and more cost-effectively than ever before.The process of CNC foam prototyping involves using specialized computer-controlled machinery to precisely cut and shape foam materials into intricate and complex forms. This process allows for the creation of highly detailed and accurate prototypes that closely resemble the finished product, without the need for expensive and time-consuming traditional manufacturing methods.One of the key advantages of CNC foam prototyping is its versatility. It can be used to create foam prototypes for a wide range of applications, from small consumer electronics to large industrial components. This flexibility has made it a popular choice for companies looking to develop new products and refine existing designs.In addition to its versatility, CNC foam prototyping also offers significant time and cost savings. Traditional prototyping methods often involve labor-intensive processes and the use of expensive materials, which can lead to long lead times and high costs. By contrast, CNC foam prototyping is a highly automated process that can quickly and accurately produce foam prototypes at a fraction of the cost of traditional methods.Moreover, CNC foam prototyping also allows for rapid iteration and refinement of designs. With the ability to quickly produce and test multiple prototypes, designers and engineers can quickly identify and address any issues or improvements, leading to a more refined and reliable final product.The team at {} has been at the forefront of this technology, continually pushing the boundaries of what is possible with CNC foam prototyping. Their dedication to innovation and continuous improvement has made them a trusted partner for companies looking to develop new products and refine existing designs.Their commitment to quality and customer satisfaction has earned them a strong reputation in the industry, and they continue to be a driving force in the development and adoption of CNC foam prototyping technology.In conclusion, CNC foam prototyping technology has revolutionized the manufacturing process, allowing for the creation of highly detailed and accurate foam prototypes with incredible speed and efficiency. {} has been a leader in this field, leveraging their state-of-the-art CNC foam prototyping facility to help their clients bring new products to market faster and more cost-effectively than ever before. With their commitment to innovation and customer satisfaction, they are poised to remain a driving force in the advancement of CNC foam prototyping technology for years to come.
Custom Metal Box Welding and Bending Service: What You Need to Know
Metal fabrication plays a crucial role in today's manufacturing and construction industries, providing the necessary components for a wide range of products and structures. One company that has been at the forefront of delivering high-quality metal fabrication services is Metal Box Welding Bending Service.Metal Box Welding Bending Service is a leading provider of metal fabrication solutions, specializing in welding, bending, and assembly services. With a strong focus on precision and quality, the company has built a reputation for delivering exceptional results to its clients.The company's state-of-the-art facilities are equipped with the latest technology and machinery, allowing them to take on projects of varying complexity and scale. Their team of skilled technicians and engineers are dedicated to meeting the unique needs of each client, ensuring that every project is completed to the highest standards.Metal Box Welding Bending Service has a diverse portfolio of clients, including those in the automotive, aerospace, and construction industries. Their ability to adapt to the specific requirements of each industry has made them a trusted partner for many businesses looking for reliable metal fabrication solutions.One of the key strengths of Metal Box Welding Bending Service is their commitment to innovation and continuous improvement. The company regularly invests in research and development to stay ahead of industry trends and maintain their competitive edge. This approach has allowed them to not only meet the current demands of their clients, but also anticipate future needs and develop new solutions to address them.Another factor that sets Metal Box Welding Bending Service apart from other metal fabrication companies is their emphasis on environmental sustainability. The company's manufacturing processes and materials are carefully selected to minimize their impact on the environment, reflecting their commitment to responsible and ethical business practices.In addition to their impressive technical capabilities, Metal Box Welding Bending Service also places a high value on customer service. They work closely with their clients throughout every step of the project, from initial design concepts to final delivery, ensuring that their needs and expectations are fully met.With their unmatched expertise and dedication to excellence, Metal Box Welding Bending Service continues to be a driving force in the metal fabrication industry, setting the standard for quality and innovation.As the demand for metal fabrication services continues to grow, Metal Box Welding Bending Service remains at the forefront of the industry, providing reliable solutions to a diverse range of clients. With their commitment to quality, innovation, and customer satisfaction, the company is well-positioned to continue leading the way in the ever-evolving world of metal fabrication.
Ultimate Guide to Laser Cutting Polyethylene Foam: Everything You Need to Know
Laser Cutting Polyethylene Foam Revolutionizes Packaging IndustryIn today's fast-paced world, businesses are constantly seeking innovative solutions to improve their products and services. One company at the forefront of this innovation is {Company name}, a leading provider of advanced packaging solutions. Recently, {Company name} has introduced a groundbreaking method for cutting polyethylene foam with laser technology, a game-changing development that is set to revolutionize the packaging industry.Polyethylene foam is widely used in packaging due to its lightweight, durable, and versatile nature. It is commonly utilized for cushioning and protecting a wide range of products during transit and storage. However, traditional methods of cutting and shaping polyethylene foam often involve time-consuming processes that are not always precise or cost-effective.{Company name} saw an opportunity to enhance the efficiency and quality of polyethylene foam cutting by leveraging state-of-the-art laser technology. By integrating laser cutting systems into their production process, they have achieved unparalleled precision, speed, and flexibility in shaping polyethylene foam, setting a new standard for the industry.The advanced laser cutting technology utilized by {Company name} allows for intricate designs and complex patterns to be effortlessly and accurately cut into polyethylene foam, providing a level of customization and detail that was previously unattainable. This capability opens up a world of possibilities for packaging designers and manufacturers, enabling them to create unique and tailored solutions to meet the specific needs of their products and customers.In addition to its precision and flexibility, laser cutting polyethylene foam offers environmental benefits as well. The process produces minimal waste and emissions, contributing to a more sustainable and eco-friendly approach to packaging production. As sustainability continues to be a key focus for businesses across the globe, this innovation aligns with the growing demand for environmentally responsible solutions.{Company name}'s investment in laser cutting technology for polyethylene foam underscores its commitment to providing cutting-edge packaging solutions to its clients. With a strong emphasis on innovation and continuous improvement, the company is dedicated to staying ahead of the curve and meeting the evolving needs of the packaging industry.This latest development further solidifies {Company name} as a leader in the packaging sector, building on its track record of delivering high-quality products and exceptional customer service. With a focus on collaboration and partnership, {Company name} works closely with its clients to understand their unique challenges and requirements, offering innovative solutions that add value and drive success.Furthermore, by incorporating laser cutting technology, {Company name} is not only enhancing the capabilities of its own manufacturing processes but also providing its clients with a competitive advantage in the market. The ability to create distinct and tailored packaging solutions through laser-cut polyethylene foam sets them apart from the competition, enabling them to stand out and make a lasting impression on their customers.Moving forward, {Company name} envisions continued advancements in laser cutting technology for polyethylene foam, ushering in a new era of possibilities for the packaging industry. With a focus on research and development, the company aims to push the boundaries of what is achievable, seeking to innovate and refine its processes to better serve its clientele.In conclusion, {Company name}'s introduction of laser cutting polyethylene foam represents a significant milestone for the packaging industry. With its unrivaled precision, flexibility, and environmental benefits, this advancement is poised to reshape the way packaging is designed and manufactured. As businesses strive to differentiate themselves in the market, the ability to leverage laser-cut polyethylene foam for customized and sustainable packaging solutions will undoubtedly be a game-changer. As {Company name} continues to lead the way in innovation, the future of packaging looks brighter than ever.
Durable and Long-Lasting Shock Absorber Rubber Stoppers for Superior Performance
[Company Introduction][Company Name] is a leading manufacturer of automotive parts and components, specializing in the production of shock absorber rubber stoppers. With a strong focus on quality and innovation, the company has established a reputation for delivering reliable and high-performance products to its customers. The company's state-of-the-art manufacturing facilities and dedicated team of engineers and technicians enable it to meet the diverse needs of the automotive industry.[News Content]The automotive industry is constantly evolving, with manufacturers striving to improve the performance, safety, and comfort of vehicles. One crucial component that plays a significant role in ensuring a smooth and stable ride is the shock absorber rubber stopper. This small but essential part is responsible for dampening the vibrations and impacts experienced by a vehicle, providing a more comfortable and controlled driving experience for the passengers.[Company Name] has been at the forefront of manufacturing high-quality shock absorber rubber stoppers, meeting the stringent requirements of the automotive industry. The company's commitment to excellence and continuous improvement has enabled it to develop innovative solutions that cater to the evolving needs of the market.The shock absorber rubber stoppers produced by [Company Name] are designed to effectively absorb and dampen the forces generated during vehicle operation, resulting in improved ride comfort and stability. The company's products are manufactured using premium quality materials that are tested for durability and performance, ensuring a long service life and reliability.One of the key factors that set [Company Name] apart from its competitors is its relentless pursuit of innovation. The company invests significantly in research and development to explore new materials and manufacturing processes, with the aim of enhancing the performance and durability of its products. This commitment to innovation has allowed [Company Name] to stay ahead of the curve and provide its customers with cutting-edge solutions that meet and exceed industry standards.In addition to its focus on product innovation, [Company Name] places a strong emphasis on quality control and assurance. Each shock absorber rubber stopper undergoes rigorous testing and inspection procedures to ensure that it meets the company's stringent quality standards. This meticulous approach to quality has earned [Company Name] the trust and confidence of its customers, who rely on the company's products to deliver consistent and reliable performance.Furthermore, [Company Name] is dedicated to sustainability and environmental responsibility. The company adheres to strict environmental regulations and adopts eco-friendly practices in its manufacturing processes. By prioritizing sustainability, [Company Name] demonstrates its commitment to creating a better and more sustainable future for the automotive industry.As the automotive industry continues to advance, the demand for high-performance and reliable shock absorber rubber stoppers is expected to grow. [Company Name] is well-positioned to meet this demand, thanks to its unwavering dedication to quality, innovation, and customer satisfaction. The company's proven track record and industry expertise make it a trusted partner for automotive manufacturers seeking top-tier components for their vehicles.In conclusion, [Company Name] remains a driving force in the automotive component industry, with its focus on innovation, quality, and sustainability. The company's shock absorber rubber stoppers are a testament to its commitment to excellence and its ability to meet the evolving demands of the automotive market. With a strong foundation built on reliability and performance, [Company Name] is poised to continue its success and make a lasting impact on the automotive industry.
High-Quality Silicone Rubber Molding for Various Applications
Silicone rubber molding is a popular and efficient manufacturing process that is used by various industries to create durable and high-quality products. This process involves using precise molds to shape and cast silicone rubber into a wide range of products, including gaskets, seals, keypads, and other custom components.One company that has become a leader in silicone rubber molding is {Company Name}. With over 20 years of experience in the industry, {Company Name} has established itself as a trusted supplier of silicone rubber products to a diverse range of clients, including those in the automotive, aerospace, medical, and consumer electronics industries. The company is known for its commitment to quality, precision, and customer satisfaction, and has earned a reputation for delivering innovative solutions to its clients' unique manufacturing challenges.At the heart of {Company Name}'s success is its state-of-the-art manufacturing facility, which is equipped with the latest technology and machinery for silicone rubber molding. The company's team of skilled engineers and technicians are experienced in working with a wide range of silicone materials, and are able to provide custom solutions to meet each client's specific requirements. Utilizing advanced CAD/CAM software, {Company Name} is able to quickly design and prototype new products, and is able to efficiently produce high volumes of precision-molded silicone components.One of the key advantages of silicone rubber molding is its ability to produce complex shapes and intricate designs with high precision and accuracy. This makes it an ideal manufacturing process for producing custom gaskets, seals, and other components that require tight tolerances and exacting specifications. Silicone rubber is also known for its excellent resistance to extreme temperatures, chemicals, and environmental conditions, making it an ideal material for a wide range of applications. From automotive gaskets to medical device components, silicone rubber molding offers a versatile and reliable solution for a variety of industries.In addition to its expertise in silicone rubber molding, {Company Name} also offers a range of value-added services to its clients, including product design and development, material selection and testing, and quality assurance and testing. The company is committed to ensuring that all of its products meet the highest standards of quality and performance, and works closely with its clients throughout the entire manufacturing process to ensure that their exact specifications are met.{Company Name} prides itself on its ability to provide innovative solutions to its clients' manufacturing challenges, and is continuously investing in new technologies and processes to further enhance its capabilities. With a focus on quality, precision, and customer satisfaction, {Company Name} is dedicated to delivering exceptional silicone rubber products that meet and exceed its clients' expectations.Overall, silicone rubber molding is a highly effective and versatile manufacturing process that offers a wide range of benefits for a variety of industries. {Company Name} has established itself as a leader in this field, and has demonstrated its expertise in delivering high-quality silicone rubber products to its clients. With its state-of-the-art facility and commitment to innovation, {Company Name} is well positioned to continue providing innovative solutions and exceptional service to its clients for many years to come.
Ultimate Guide to Injection Molds: Everything You Need to Know
Injection Molds: Driving Innovation in the Manufacturing IndustryInjection molding is a widely used manufacturing process in which molten material is injected into a mold, allowing it to cool and solidify into a specific shape. This process is essential in the production of a vast array of everyday items, ranging from plastic packaging to automotive parts and medical devices. One company that has been at the forefront of injection mold technology is {}.{} is a leading provider of injection molds, with a strong focus on innovation and precision engineering. The company has built a solid reputation for delivering high-quality molds that meet the diverse needs of its clients across various industries. With state-of-the-art facilities and a team of experienced professionals, {} has been able to stay ahead of the competition by consistently pushing the boundaries of what is possible in injection molding.One of the key factors that sets {} apart from its competitors is its commitment to research and development. The company invests heavily in the latest technologies and equipment to ensure that its molds are at the cutting edge of the industry. This dedication to innovation has allowed {} to develop a wide range of molds that can be customized to meet the specific needs of its clients, no matter how complex or demanding their requirements may be.In addition to its innovative approach, {} also places a strong emphasis on quality control. The company has stringent quality assurance processes in place to ensure that every mold that leaves its facility meets the highest standards. This commitment to quality has earned {} the trust and loyalty of its clients, who rely on the company to deliver molds that are not only precise and durable but also cost-effective.Furthermore, {} is also known for its excellent customer service. The company works closely with its clients throughout the entire process, from the initial concept and design stage to the final production of the molds. This collaborative approach allows {} to gain a deep understanding of its clients' needs and to provide them with tailored solutions that perfectly align with their requirements.One of the most significant developments in injection mold technology in recent years has been the rise of 3D printing. {} has been quick to embrace this technology and has integrated it into its manufacturing processes. This has allowed the company to produce molds with even greater precision and intricacy, opening up new possibilities for its clients in terms of design and functionality.Looking to the future, {} remains committed to driving innovation in the injection molding industry. The company is constantly exploring new materials, techniques, and technologies to further enhance the performance and capabilities of its molds. By staying at the forefront of these advancements, {} is well-positioned to continue meeting the evolving needs of its clients and maintaining its position as a leader in the industry.In conclusion, injection molds are a critical component of the manufacturing process, and {} has established itself as a leading provider of high-quality, innovative molds. With its focus on research and development, quality control, and customer service, the company has earned the trust and loyalty of its clients across various industries. As it continues to push the boundaries of what is possible in injection molding, {} is poised to drive further innovation in the industry and meet the ever-changing needs of manufacturers around the world.